Table of Contents
G5 Ultra Overview
Granule printing, or Fused Granular Fabrication (FGF), has long been a staple in industrial printing due to its cost-effectiveness. However, its accessibility to hobbyists and prosumers has been limited by the high cost of granule extruder systems. The original G5 made pellet printing accessible, and the new G5 Ultra makes it a whole lot better.
The G5 Ultra still maintains a similar build volume as the first (500×500x400mm), but doubles down on speed, particularly the print speed and the material deposition rate. While the first G5 was capable of printing at 100 mm/s, the new G5 Ultra churns out molten plastic at a hefty 220mm/s. With regards to the flow rate of the materials, the G5 Ultra is capable of depositing a staggering 0.8kg per hour.
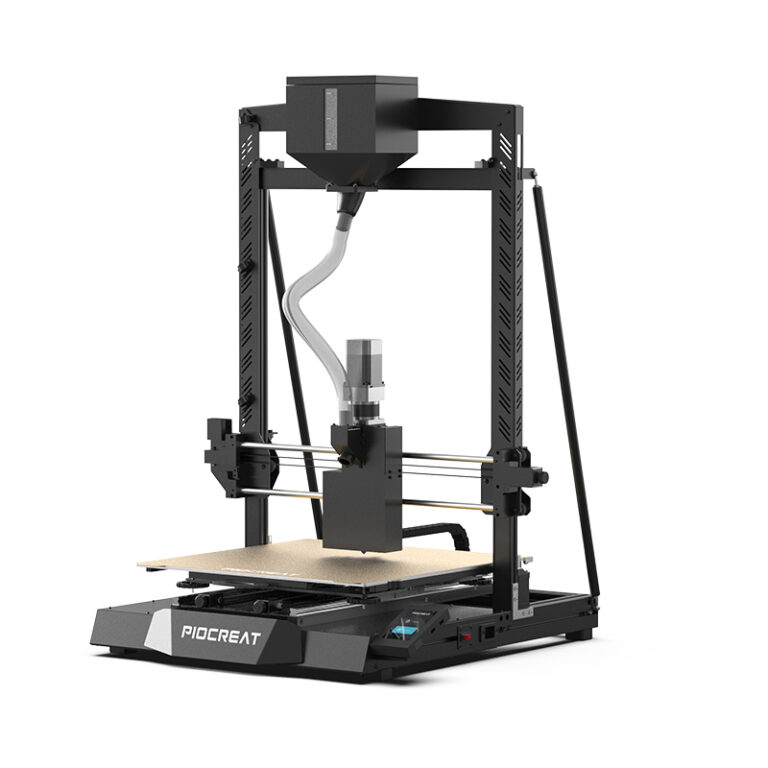
Feeding and Extruding
The next generation extruder (with segmented heat zones) can fit nozzles in diameters ranging from 0.4mm up to 3mm, and the machine can print pellets/granules measuring 2-5mm in diameter. The particles are fed into the extruder from a 3 liter hopper, ensuring a ready supply of feedstock for its huge deposition rate. It heats up to a toasty 400°C, enabling the printing of a wide range of materials.
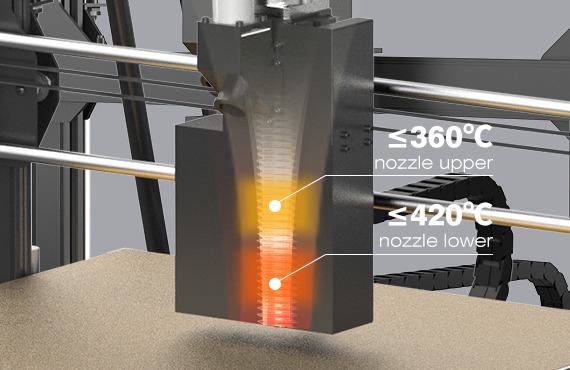
And what if your print does run out of material during a job? Well, Piocreat has thought of this possibility and developed a new material level sensor. The sensor detects when material is running out, and sounds a warning alarm, notifying users to refill the hopper. The printer keeps the progress of the interrupted print job in memory, and resumes from exactly where it stopped, once the pellets have been refilled.
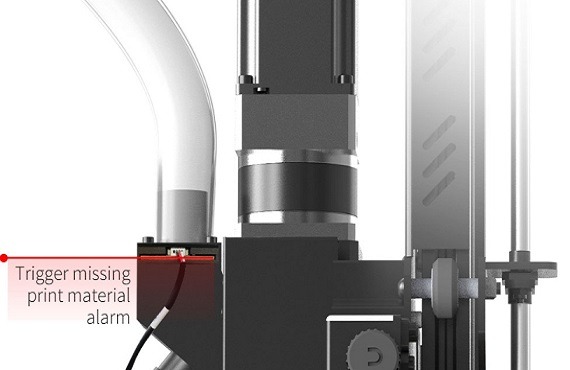
Another upgrade to the G5 Ultra is the firmware. While the original G5 was based on Marlin, the G5 Ultra is installed with Klipper, allowing a whole bunch of new features, including the ability to send files and monitor prints via WiFi.
And of course, as well as the new capabilities, the G5 Ultra retains several features from the original machine, including dual Z-axis lead screws with dual tie rods, all mounted to its sturdy metal frame, to provide extra stability while printing.
Pellets – The Feedstock of the Future
So, we have seen how the G5 Ultra is a serious upgrade to the original machine.
Let’s just have a quick reminder as to why pellets are indeed the future, and why we should all be moving away from filament as quickly as humanly possible.
Cost
First up, the price of pellets is vastly cheaper when compared to the price of filaments. Filaments come from pellets after all, and require processing to get to the filament state. Filaments are more costly to store, and transport, and all of these extra processes add up, and ultimately, hit the customer’s pocket. Pellets are cheaper. That’s a fact.
Environment
Pellets are less energy intensive to produce, easier to transport in bulk (meaning lower transport emissions), and don’t come in wasteful plastic spools. In addition, there are many recycled pellets on the market, and if you have the means to shred your own plastics, you can also recycle your own waste into feedstock.
Material variety
With its ability to heat up to 400°C, the G5 Ultra Pellet 3D Printer excels in processing a wide range of thermoplastics and composites. This flexibility allows for experimenting with various pellets, including PLA\PC\ABS\PETG\PETG-GF/PP/TPU/PA-CF/ABS-CF/PC-CF, and more.
Conclusion
We recommends using original materials for optimal material properties, ensuring enhanced performance of printed components with superior quality.
So to sum it all up, the G5 Ultra allows cheaper printing, is more environmentally friendly, and thanks to its huge build volume and flow rate, allows you to print massive items very quickly indeed. What’s not to like?