Fused Granulate Fabrication (FGF) 3D printing is a powerful manufacturing process that utilizes plastic pellets as its primary material source. This approach, distinct from filament-based 3D printing, feeds granulated thermoplastic pellets into an extruder where they are melted and deposited layer by layer to form the final object. This method is highly efficient for large-scale production, reducing both material costs and production time, especially for industrial applications.
In this blog post, we’ll compare four popular materials used in FGF 3D printing — PETG, ABS, TPU, and PLA pellets. We’ll evaluate each based on factors like printability, strength, resistance to elements, flexibility, temperature resistance, and environmental impact, so you can make an informed choice for your projects.
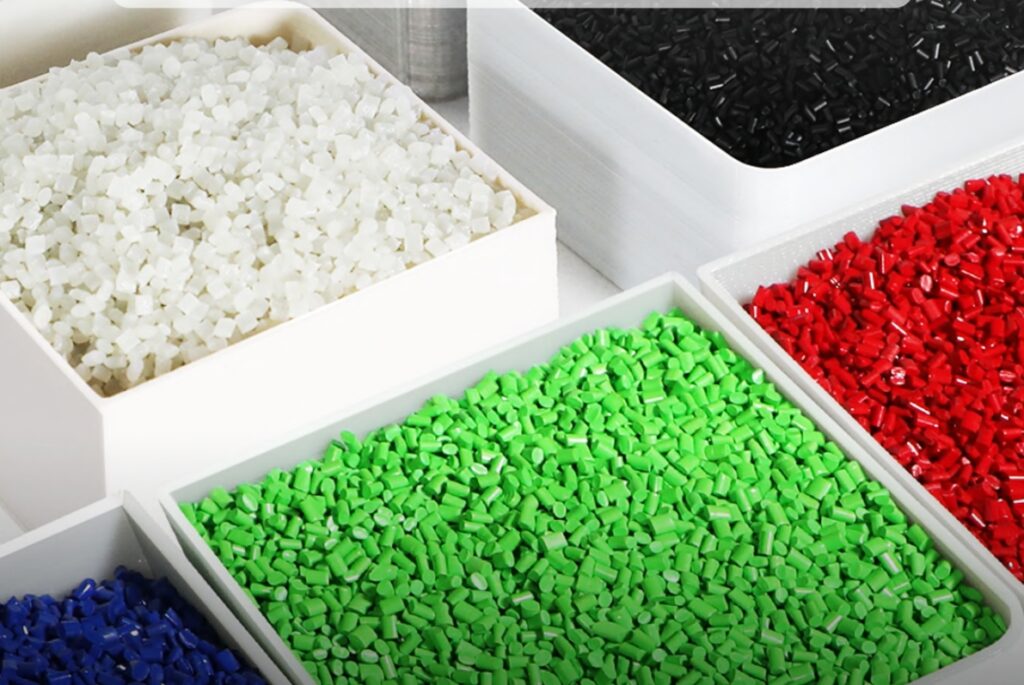
Popular FGF 3D Printing Materials
1. ABS Pellets
Acrylonitrile Butadiene Styrene (ABS) is a popular engineering thermoplastic known for its strength, durability, and impact resistance. It is commonly used in automotive parts, consumer goods, and industrial applications due to its reliability and mechanical properties. ABS is particularly popular in FGF printing because it’s relatively affordable and can be used for high-stress applications.
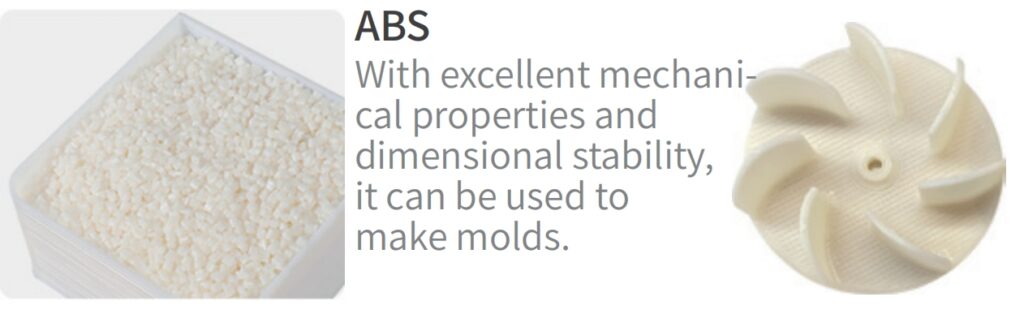
2. PETG Pellets
Polyethylene Terephthalate Glycol (PETG) is a versatile material that combines the strength and durability of ABS with the ease of use associated with PLA. PETG is known for its good chemical resistance and weather durability, making it an excellent choice for parts exposed to elements or chemicals. PETG’s transparent or translucent properties also make it popular for aesthetic or functional components where visibility is key.
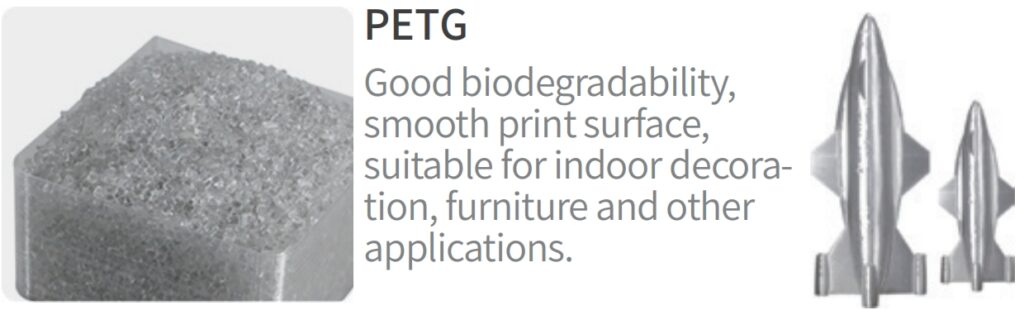
3. TPU Pellets
Thermoplastic Polyurethane (TPU) is a flexible, elastic material with rubber-like properties, making it ideal for parts that require high flexibility and durability. TPU is commonly used in products like protective cases, seals, gaskets, and various wearable components. The elasticity of TPU makes it unique among FGF materials, and it’s ideal for parts that require shock absorption or repeated bending without breaking.
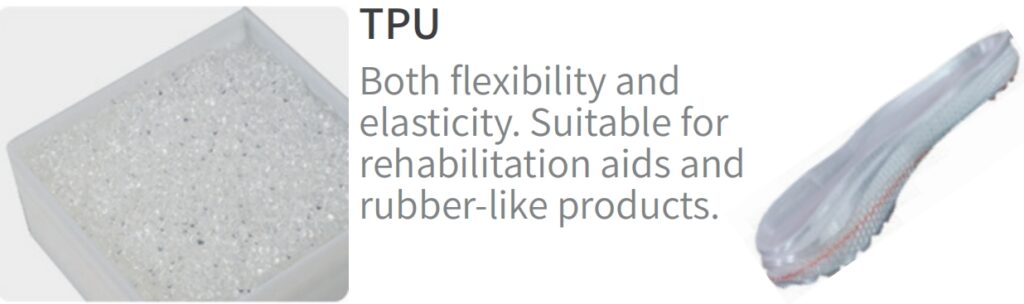
4. PLA Pellets
Polylactic Acid (PLA) is a biodegradable thermoplastic derived from renewable resources such as corn starch or sugarcane. PLA is well-suited for beginner projects or applications where environmental impact is a concern. Although PLA is less durable than ABS or PETG, it is easier to print, has minimal warping, and emits fewer fumes, making it suitable for non-technical applications and educational projects.
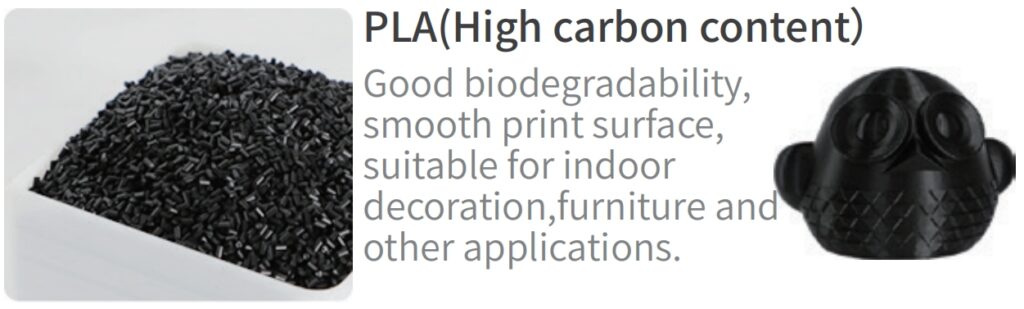
Comparing ABS, PETG, TPU, and PLA Pellets for FGF 3D Printing
Let’s explore each material’s characteristics in greater detail and see how they stack up for various applications in FGF 3D printing.
1. Printability
ABS: Known for its tendency to warp during printing, ABS requires a heated bed and controlled environment to prevent warping and layer separation. ABS can be challenging for beginners but yields strong, durable parts when printed properly.
PETG: PETG is generally easy to print with FGF technology and has minimal warping issues compared to ABS. It is also less prone to odors, making it a popular choice for indoor settings and educational environments.
TPU: TPU’s flexibility can make it challenging to print, as it requires precise control over extrusion and print speed. TPU is better suited for intermediate to advanced users who need flexible parts and have experience with FGF printing.
PLA: PLA is one of the easiest materials to print, with minimal warping and no need for a heated bed, making it ideal for beginners. It’s forgiving to common issues, such as layer adhesion, that can occur in other materials.
Best for Printability: PLA and PETG, due to their minimal warping and ease of use.
2. Strength
ABS: Known for its high impact resistance and strength, ABS is suitable for functional prototypes and durable components. Its toughness makes it a popular choice for automotive and industrial parts.
PETG: PETG provides a balance of strength and flexibility, making it suitable for applications that require durability with a bit of flexibility, such as packaging and storage containers.
TPU: While TPU is not “strong” in the traditional sense, its tensile strength is significant, allowing it to absorb impact and stretch without breaking. TPU is best for parts requiring resilience rather than rigid strength.
PLA: PLA has lower strength than ABS and PETG, making it less suitable for high-stress applications. It’s better suited for aesthetic, low-impact parts or disposable components.
Best for Strength: ABS and PETG, with ABS being particularly robust for high-stress applications.
3. Resistance to Elements
ABS: ABS is moderately resistant to water and chemicals but can degrade under prolonged UV exposure, limiting its use for outdoor applications.
PETG: PETG’s chemical and water resistance make it ideal for outdoor and industrial applications, where it may be exposed to moisture or chemicals. It retains its properties even in humid or slightly corrosive environments.
TPU: TPU is highly resistant to oils, greases, and chemicals, making it well-suited for parts in industrial settings. However, TPU is less resistant to extreme heat and prolonged UV exposure.
PLA: PLA is not resistant to water or chemicals and can degrade when exposed to sunlight and moisture. It is better suited for indoor applications.
Best for Resistance to Elements: PETG, followed by TPU for industrial applications requiring chemical resistance.
4. Flexibility
ABS: ABS has limited flexibility and tends to be rigid, making it best for parts that need durability but not elasticity.
PETG: PETG offers some flexibility while remaining strong, allowing it to handle minor impacts without breaking. It’s suitable for applications that need a balance between rigidity and flexibility.
TPU: TPU is highly flexible, with rubber-like properties. It’s ideal for applications needing repeated bending, like gaskets, seals, and flexible housings.
PLA: PLA is quite rigid and brittle, making it unsuitable for parts that require flexibility or impact resistance.
Best for Flexibility: TPU, as it offers the highest elasticity and resilience.
5. Temperature Resistance
ABS: ABS can withstand moderate temperatures, making it suitable for parts that may experience some heat but not extreme conditions.
PETG: PETG has good thermal resistance, often outperforming PLA but falling short of ABS. It can withstand moderate heat, making it suitable for most applications but not high-temperature environments.
TPU: TPU has lower heat resistance, making it unsuitable for applications that involve sustained high temperatures.
PLA: PLA has the lowest heat resistance and can warp at temperatures as low as 60°C. It’s best for ambient temperature use.
Best for Temperature Resistance: ABS, as it maintains stability in moderate temperature conditions.
6. Biodegradability and Recyclability
ABS: ABS is not biodegradable, but it can be recycled. However, recycling facilities for ABS may not be available everywhere.
PETG: PETG is not biodegradable, but it is recyclable, and many facilities accept PETG due to its compatibility with PET recycling processes.
TPU: TPU is generally not biodegradable, and recycling options are limited, as it requires specialized facilities.
PLA: PLA is biodegradable under industrial composting conditions, making it the most environmentally friendly option of the four materials. However, it still requires specific conditions to break down fully.
Best for Biodegradability and Recyclability: PLA for biodegradability; PETG and ABS for recyclability.
Summary Table
Material | Printability | Strength | Element Resistance | Flexibility | Temperature Resistance | Sustainability |
---|---|---|---|---|---|---|
ABS | Moderate | High | Moderate | Moderate | High | Recyclable |
PETG | Easy | High | High | Moderate | Moderate | Recyclable |
TPU | Challenging | Moderate | Very High | High | Moderate | Recyclable |
PLA | Easy | Moderate | Low | Low | Low |
Choosing the Right Material for FGF 3D Printing
Each of these materials — ABS, PETG, TPU, and PLA — offers unique benefits for FGF 3D printing applications:
- ABS is ideal for durable, high-strength parts in moderate-temperature settings, such as automotive and industrial components.
- PETG offers balanced strength, chemical resistance, and ease of use, making it suitable for both indoor and outdoor applications.
- TPU is the best choice for flexible parts, shock absorption, and wear resistance in industrial or consumer applications.
- PLA is an eco-friendly, easy-to-print option best suited for non-technical or aesthetic projects.
Selecting the right material depends on the specific requirements of your project, such as strength, flexibility, environmental exposure, and sustainability goals.