Table of Contents
3D printing technology has revolutionized manufacturing, and understanding the differences between Fused Granulate Fabrication (FGF) and Fused Filament Fabrication (FFF) is crucial for choosing the right method for your projects. This article delves into the unique properties, applications, and cost considerations of FGF and FFF 3D printing techniques.
What is FGF 3D Printing?
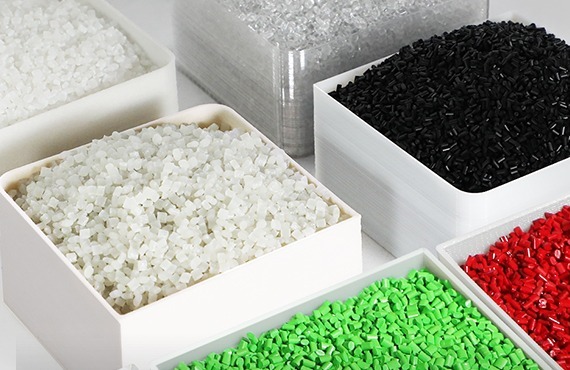
Fused Granulate Fabrication (FGF) is a 3D printing technology that uses plastic pellets as the primary material. This method involves feeding granulated thermoplastic into an extruder, which melts the granules and deposits the molten material layer by layer to create the final object. FGF is known for its ability to print large-scale objects quickly and affordably, making it ideal for industrial applications.
FGF stands out because it can utilize a wide variety of thermoplastic materials, including recycled plastics, which significantly reduces material costs. The use of pellets instead of filaments allows for high throughput, making FGF suitable for large-scale production. Additionally, the ability to use recycled and lower-cost materials makes FGF an environmentally friendly and economically viable option for many manufacturers.
What is FFF 3D Printing?
Fused Filament Fabrication (FFF), also known as Fused Deposition Modeling (FDM), is a more common 3D printing technique that uses spooled filaments of plastic as the feedstock. The filament is fed into a heated nozzle, melted, and extruded to build the object layer by layer. FFF is widely used due to its simplicity, accessibility, and versatility.
FFF printers are popular for producing detailed, high-resolution prints. They are suitable for a wide range of applications, from prototyping to small-batch production. The variety of available filaments, such as PLA, ABS, PETG, and specialty materials, adds to the versatility of FFF printing. Furthermore, the ease of use and widespread availability of FFF printers and filaments make them an excellent choice for hobbyists, educational institutions, and professional applications alike.
What is the Difference Between FGF and FFF?
Print Resolution
When comparing FFF vs. FGF, print resolution is a critical factor. FFF typically offers higher print resolution and finer detail, making it ideal for applications requiring precision and intricate designs. The smaller nozzle sizes and controlled filament feed in FFF printers allow for detailed prints with smooth surfaces. This makes FFF suitable for producing small, detailed prototypes, models, and parts with complex geometries.
In contrast, FGF printers, while capable of producing large objects, generally have lower resolution due to the larger nozzle sizes and higher material flow rates. This makes FGF more suitable for large, less detailed prints where speed and material cost are more important than fine detail. However, advancements in FGF technology are continually improving the resolution and surface finish of printed parts, expanding its potential applications.
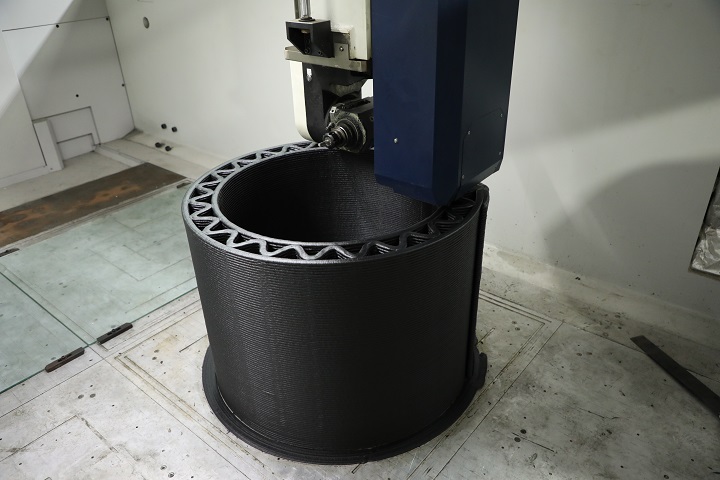
Print Speed
Print speed is another important consideration in the FFF vs. FGF debate. FGF printers can produce large parts much faster than FFF printers. The use of granulated feedstock and high-flow extrusion systems allows FGF printers to deposit material quickly, significantly reducing print times for large objects. This makes FGF an attractive option for industries needing rapid production of large components, such as automotive, aerospace, and construction.
FFF printers, while slower in producing large parts, excel in printing smaller, high-resolution objects. The controlled extrusion process ensures detailed prints but at a slower rate compared to FGF. This makes FFF ideal for applications where detail and surface finish are more critical than speed, such as in the production of prototypes, functional parts, and consumer products.
Material Compatibility
Material compatibility is a major advantage of FGF 3D printing. FGF printers can use a wide range of thermoplastic materials, including recycled plastics and more affordable pellets. This flexibility makes FGF an economical choice for large-scale production and environmentally friendly projects. Additionally, the ability to use various types of granulates, including high-performance engineering plastics, expands the application possibilities for FGF.
FFF printers also offer a broad range of materials, but they are limited to filament form. While many specialty filaments are available, the cost per kilogram is generally higher than that of pellets used in FGF. However, FFF printers excel in producing prints with specific material properties required for various applications. The diversity of filaments, including composites and flexible materials, allows for tailored solutions in industries such as healthcare, automotive, and consumer goods.
Best Pellet 3D Printers
When considering the best pellet 3D printers for FGF, the following models stand out for their capabilities and performance.
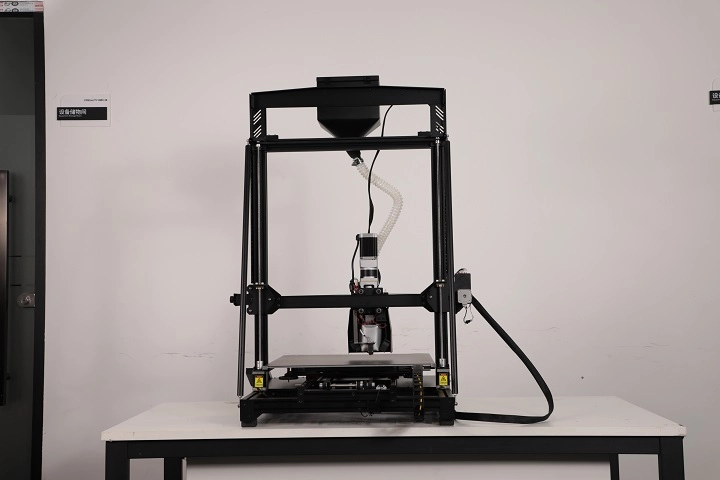
G5Ultra Pellet 3d printer
- Printing Size: 500*500*400mm
- Features:
- Nozzle temperature up to 400℃
- Rapid heating of hot bed up to 120℃
- Suitable for more materials
- High-speed printing
The G5Ultra is a high-speed industrial pellet 3D printer designed for desktop use. It utilizes low-cost thermoplastic pellet feedstocks, making it an economical choice for various applications. The G5Ultra’s high-speed printing capabilities and versatility in material use make it ideal for small to medium-sized parts. This printer is particularly suitable for businesses and research institutions looking to explore pellet 3D printing without the need for large, industrial-scale equipment.
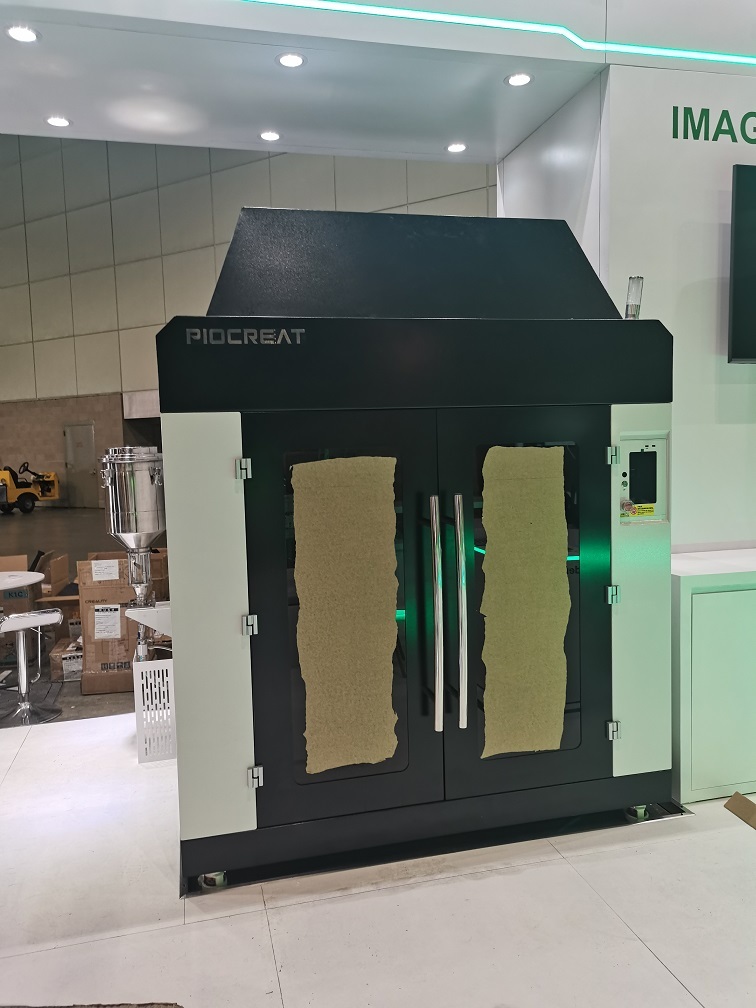
G12 Pellet 3d printer
- Printing Size: 1200*1000*1000mm
- Features:
- Nozzle temperature up to 450℃
- Rapid heating of hot bed up to 120℃
- High Flow Screw Extrusion
- Powerful Servo Motor
The G12 is a large-format pellet extrusion printer capable of printing medium-to-large format parts. Its robust design and high-performance features make it suitable for industrial applications requiring large, durable parts. The high flow screw extrusion and powerful servo motor ensure efficient and consistent printing performance. The G12 is an excellent choice for industries such as automotive, aerospace, and construction, where the production of large, high-strength parts is essential.
Wrapping Up
Fused Granulate Fabrication (FGF) and Fused Filament Fabrication (FFF) offer distinct advantages depending on the application. FGF is ideal for large-scale, cost-effective production with a wide range of materials, while FFF excels in producing high-resolution, detailed prints for smaller objects. Understanding the differences between these technologies helps in selecting the right method and equipment for your specific needs.
Whether you need the versatility and detail of FFF or the cost-effectiveness and speed of FGF, the advancements in 3D printing technology provide a solution for nearly every manufacturing challenge. With top-tier pellet 3D printers like the G5Ultra and G12, businesses can leverage the benefits of FGF to enhance their production capabilities and drive innovation.
FGF and FFF technologies continue to evolve, with ongoing research and development aimed at improving their capabilities and expanding their applications. As these technologies advance, they will become increasingly accessible and affordable, enabling more industries to benefit from the unique advantages of 3D printing. Whether you’re looking to produce large, cost-effective parts with FGF or high-resolution, detailed components with FFF, understanding the strengths and limitations of each technology will help you make informed decisions and achieve your manufacturing goals.