3D Printing Custom Ear Molds: Benefits in Hearing Healthcare
piocreat3d
on
November 6, 2024
3D printing has brought about significant advancements in audiology, particularly in the production of custom ear molds. Traditionally, the process of manufacturing ear molds was labor-intensive, with a high margin for error, often leading to a time-consuming and costly trial-and-error approach. However, 3D printing is transforming this field by enabling audiologists to produce custom ear molds with greater precision, efficiency, and scalability.
In this post, we’ll discuss the benefits of 3D printing custom ear molds, explore how this technology is improving hearing healthcare, and introduce the best Piocreat 3D printers designed for custom-fit ear molds and hearing devices.
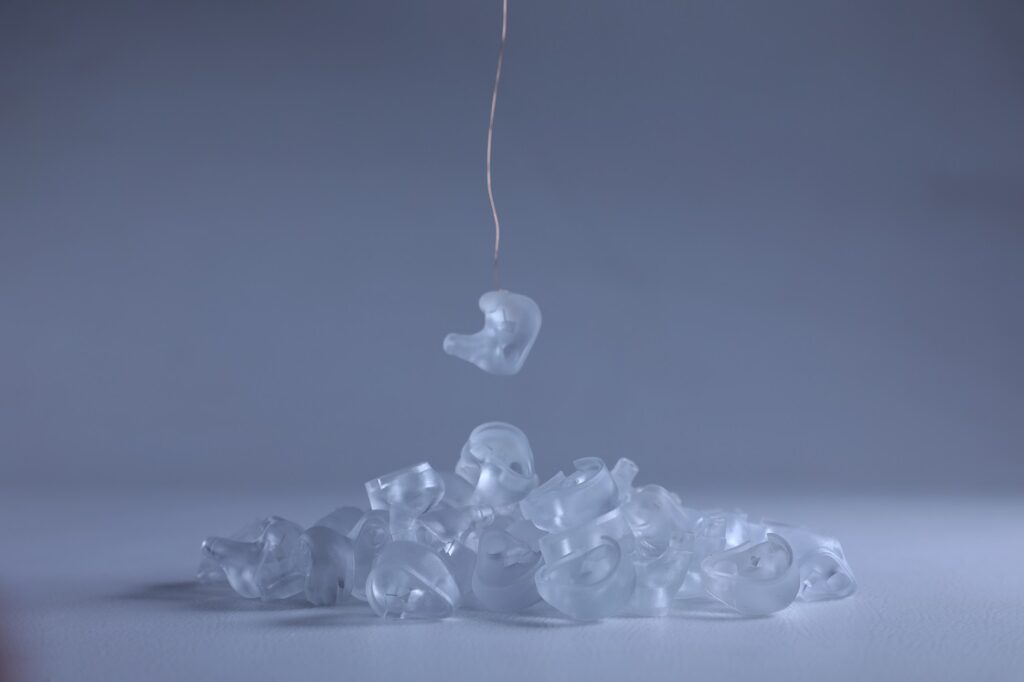
3D Printing Custom Ear Molds: A Game Changer in Audiology
Producing custom ear molds requires a high degree of accuracy and fit, as even minor discrepancies can lead to discomfort or compromised device performance. Traditional methods relied on manual craftsmanship, which limited precision and often led to inconsistencies. Digital manufacturing with 3D printing, however, captures the exact dimensions of each patient’s ear canal, ensuring that ear molds fit perfectly and comfortably.
While access to 3D printing for ear molds was initially limited to large laboratories, the recent availability of desktop LCD and DLP 3D printers is making it possible for audiologists and small businesses to adopt this technology. With affordable, compact 3D printers, clinics of all sizes can now create ear molds quickly, enhancing their ability to provide quality care while reducing production costs.
Key Benefits of 3D Printing in Hearing Healthcare
Precision
In hearing healthcare, precision is paramount. Even a slight variation in an ear mold can impact a device’s effectiveness or the wearer’s comfort. 3D printing offers unmatched accuracy, allowing audiologists to capture the fine details of each ear canal and replicate them exactly. This level of precision not only reduces the need for adjustments but also enhances the device’s performance, creating a more comfortable experience for the patient.
With digital scans and 3D printing, audiologists can produce ear molds that require fewer adjustments, minimizing the chances of refits and remakes. Patients benefit from improved comfort and device functionality, while clinics and labs benefit from lower production costs and faster turnaround times.
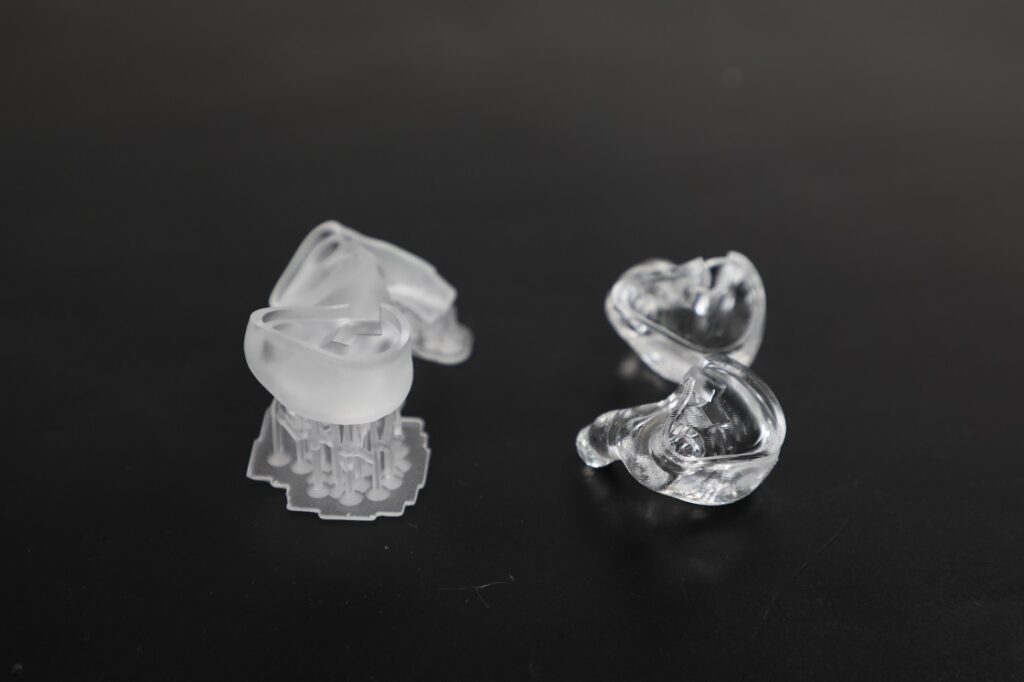
Digital Agility
The digital workflow enabled by 3D printing provides significant flexibility for hearing healthcare providers. Instead of relying on physical molds, audiologists can store digital files of each patient’s ear anatomy, allowing for easy reprints or modifications without the need for a new scan. This agility is particularly useful for patients who need multiple ear molds or modifications over time, as adjustments can be made directly to the digital file and printed as needed.
Digital agility also simplifies record-keeping, making it easy to retrieve patient data for future adjustments or device upgrades. This streamlined workflow reduces production times and enables more efficient management of each patient’s unique needs.
Customization
TPU, a popular material used in 3D printing ear molds, is highly flexible and durable, offering comfort and a secure fit. With 3D printing, each ear mold is tailored precisely to the individual’s ear, creating a snug, secure fit that reduces sound leakage and maximizes hearing device performance. TPU’s durability ensures that the ear molds can withstand daily wear and tear, maintaining their shape and functionality over time.
This custom-fit experience extends beyond ear molds to include other hearing-related products, such as ear shells and hearing protection devices. With 3D printing, audiologists can offer patients products that are not only comfortable but also highly effective.
Piocreat 3D Printers for Custom Ear Molds and Hearing Devices
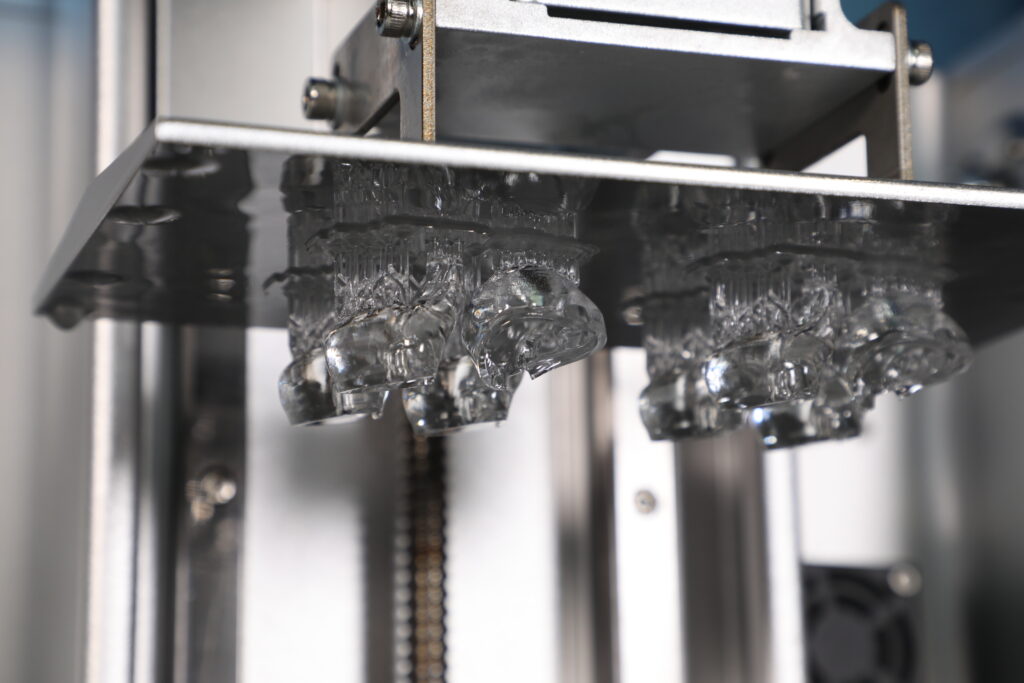
Piocreat offers a range of 3D printers optimized for creating custom-fit hearing devices, earmolds, ear shells, and hearing protection devices. Each printer is designed to meet the high precision requirements of audiology applications, providing consistent, high-quality results.
1. DJ89 PLUS: High-Resolution LCD Printer for Custom Ear Molds
The DJ89 PLUS is an 8K 10.3″ LCD 3D printer known for its unmatched print clarity and detail, making it ideal for audiology applications. This cost-effective printer is designed to produce highly detailed custom ear molds, ensuring that each piece captures the intricacies of the patient’s anatomy.
Key Features of DJ89 PLUS:
- 29μm Pixel Size: High resolution ensures that each ear mold captures even the finest details for a perfect fit.
- Heating Chamber: Maintains a stable resin temperature, which enhances the quality of each print by preventing warping or inconsistencies.
- Automatic Feeding: Streamlines the printing process, reducing manual intervention and ensuring a smoother workflow.
- Stable Z-axis Structure: Ensures high stability and accuracy, essential for producing consistently precise ear molds.
The DJ89 PLUS is an excellent choice for small clinics and labs looking for an affordable, reliable solution for high-quality custom ear molds.
2. D158: Compact DLP Printer for High Precision and Reliability
The D158 is a compact DLP 3D printer that uses Texas Instruments technology for precision and reliability, making it a practical solution for dental and audiology applications alike. Its compact size makes it easy to integrate into any clinic or lab, while its advanced features make it suitable for a variety of custom ear molds.
Key Features of D158:
- Automatic Lifting Cover: Protects prints from dust and other contaminants, ensuring quality results.
- 62μm Pixel Size: Provides the detail necessary for complex models, ensuring the highest degree of accuracy.
- High-Speed Release Film: Accelerates the printing process without sacrificing detail, making it ideal for rapid production.
- Stable Z-axis Structure: Supports the printer’s ability to produce consistent, accurate prints.
The D158 is ideal for labs and clinics that need high-quality custom ear molds but may be limited on space. Its precision and compact design make it a versatile choice.
3. D150: High-Speed DLP Printer for Maximum Productivity
The D150 is designed for high productivity, with printing speeds up to 80mm/h, making it ideal for labs that require quick turnaround times. With adjustable light intensity and a durable light engine, the D150 is perfect for producing large batches of custom ear molds efficiently.
Key Features of D150:
- Speeds up to 80mm/h: Enables fast production, reducing wait times for patients and boosting clinic efficiency.
- High-Speed Release Film: Allows for smooth layer release, speeding up the overall printing process.
- Adjustable Light Intensity (6000-20000uw/cm2): Offers customization based on the specific resin or model requirements, ensuring high-quality output.
- Light Engine Life of 30,000+ Hours: Ensures reliable, long-term performance, minimizing maintenance needs and operational costs.
The D150’s speed and quality make it ideal for high-volume clinics or labs that need fast, accurate results.
Conclusion
3D printing has transformed the production of custom ear molds, allowing for unparalleled accuracy, comfort, and efficiency in hearing healthcare. By utilizing 3D printing, audiologists can create custom-fitted devices that enhance the patient experience while reducing production costs and turnaround times.
Piocreat’s DJ89 PLUS, D158, and D150 3D printers each offer distinct advantages, from high-resolution output to speed and productivity, making them excellent choices for clinics and labs looking to adopt digital manufacturing. With these 3D printers, audiology professionals can bring the latest technology into their practices, improving patient care and streamlining operations.
Whether you’re a beginner or an expert in 3D printing, the capabilities of these devices enable businesses of all sizes to embrace digital workflows, enhancing both the quality and accessibility of custom ear molds and hearing protection solutions. By investing in the right 3D printer, hearing healthcare providers can stay ahead of the curve and provide patients with comfortable, effective, and custom-fit solutions that make a lasting difference.