Piocreat’s Formnext SOUTH CHINA 2024: New Product Launches and Innovative Technologies
piocreat3d
on
August 30, 2024
Piocreat is thrilled to announce the successful conclusion of our participation at Formnext SOUTH CHINA 2024! From August 28th to 30th, 2024, we had the privilege of showcasing our latest innovations at the Shenzhen International Convention and Exhibition Center, Booth C194. The event was a tremendous success, and we are excited to share the highlights with you!
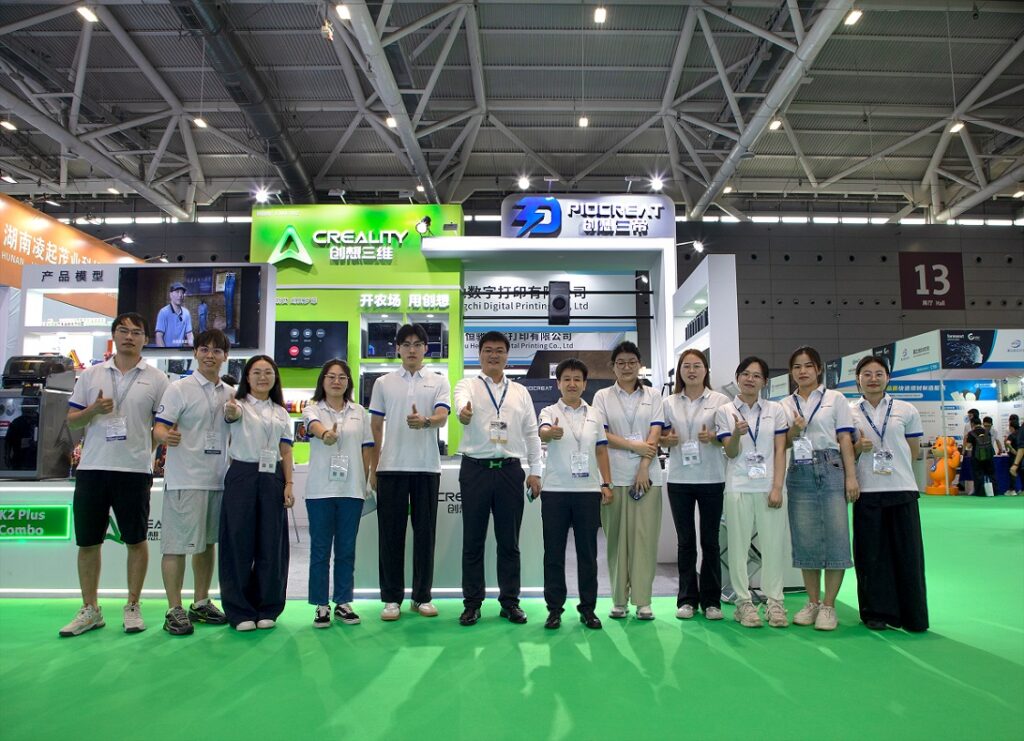
Highlights from Booth C194
Dental 3D Printing Solutions
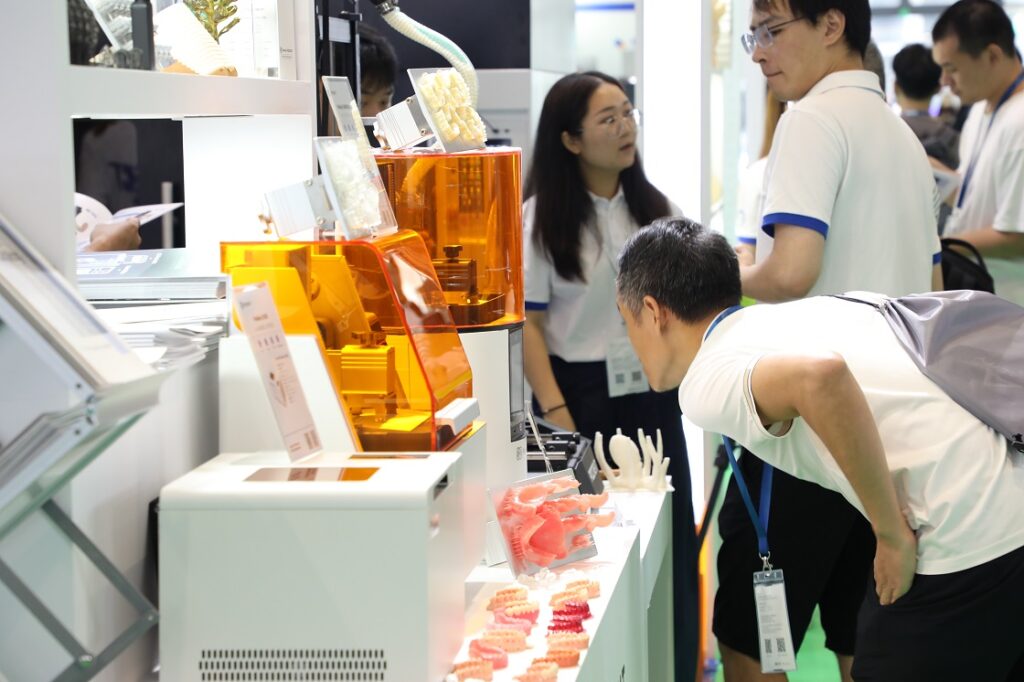
At Formnext SOUTH CHINA 2024, Piocreat’s booth was a hub of activity, with our cutting-edge dental 3D printing solutions capturing the attention of industry professionals:
DJ89 PLUS Resin 3D Printer: This advanced printer, designed specifically for dental applications, features an integral light source that ensures 90% light uniformity. With an 8K 10.3″ LCD, 29μm pixel size, heating chamber, automatic feeding, and a stable Z-axis, the DJ89 PLUS delivers precise, high-quality dental models efficiently and cost-effectively.
D158 Compact DLP 3D Printer: Perfect for dental labs, orthodontics, and practices, the D158 offers precision and reliability in a compact design. Key features include an automatic lifting cover, 62μm pixel size, high-speed release film, and a stable Z-axis structure, making it an ideal choice for dental professionals seeking simplicity and accuracy.
UV02 Post-Processing Tool: Designed specifically for professional dental resins, the UV02 offers controlled light for perfect curing in just 1-5 minutes, ensuring top-notch results for dental applications.
Innovative Large-Scale 3D Printing Solutions
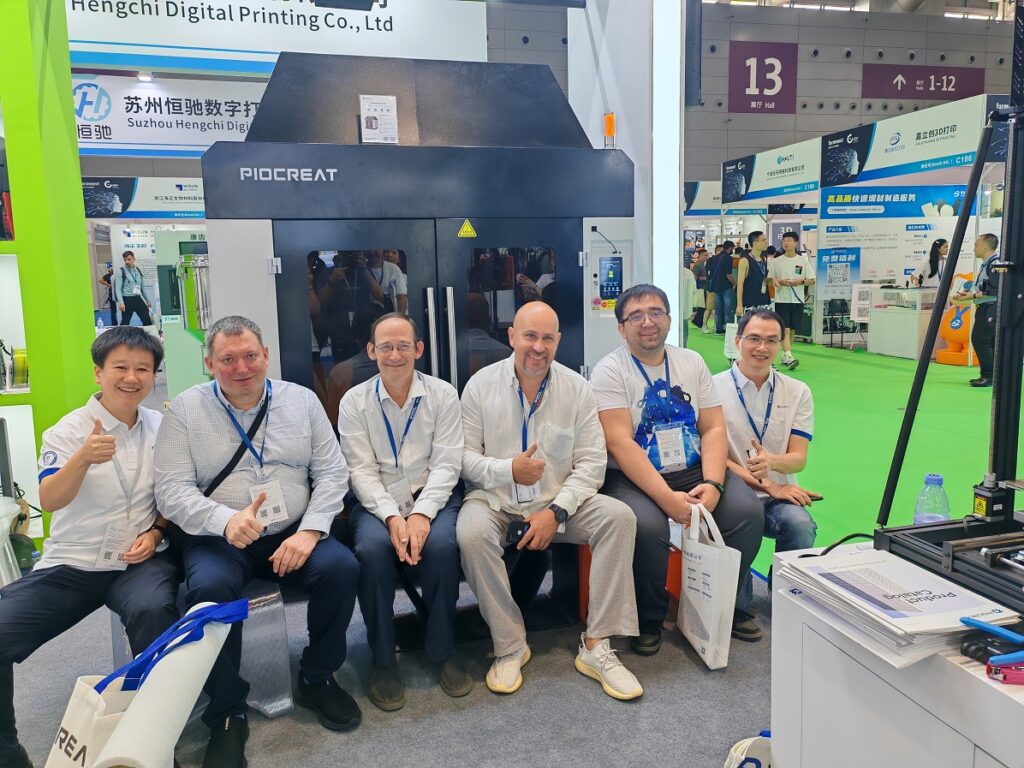
In addition to our dental solutions, Piocreat also showcased our large-scale 3D printing capabilities:
- G12 Pellet 3D Printer: This powerful machine boasts a massive 1200*1000*1000mm build size, with a 450°C nozzle, 120°C rapid hot bed heating, high flow screw extrusion, and a robust servo motor. The G12 is designed to handle large-format printing projects with precision and efficiency.
Exciting New Product Launch
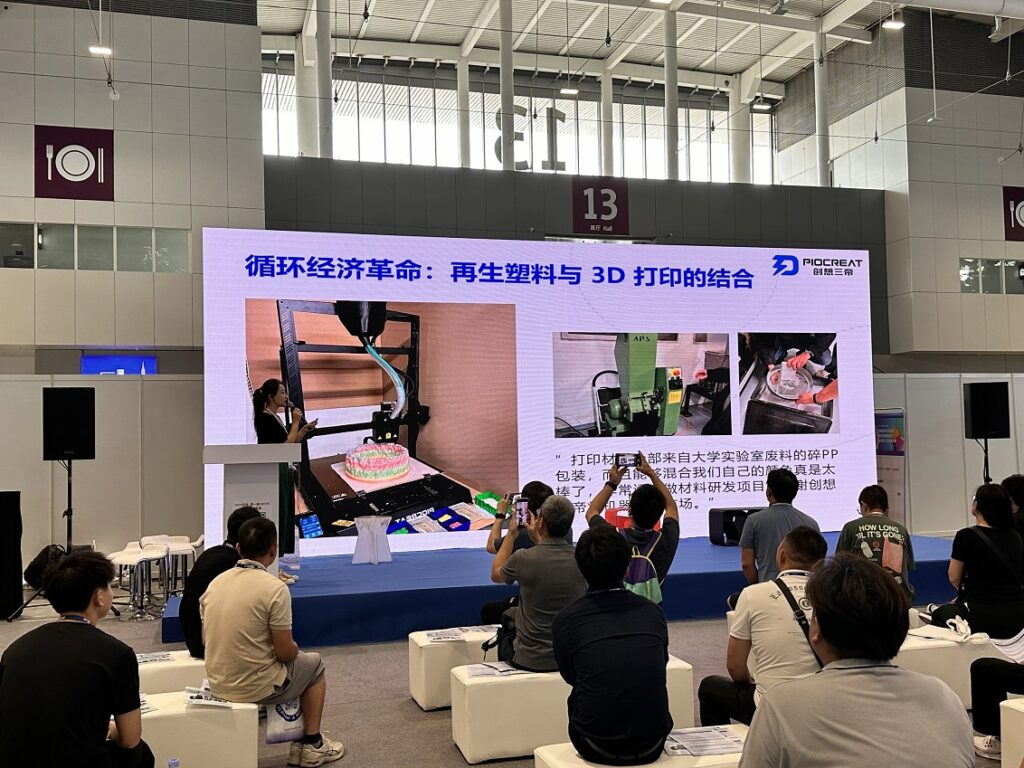
One of the most anticipated moments at Formnext SOUTH CHINA 2024 was Piocreat’s new product launch. We proudly introduced the Heavily Upgraded G5Ultra Pellet 3D Printer—an advanced desktop industrial production system. This new model features significant enhancements, including:
- Intelligent Laser Ranging with 64-Point Leveling Technology: Replacing the CR Touch, this new system ensures precise leveling for improved print quality.
- High-Speed Motors: The upgraded motors significantly boost printing speed, making the G5Ultra faster and more efficient than ever before.
- High Precision Guide Rails: These new rails provide increased stability during printing, resulting in higher quality output.
- Upgraded Slicing Software: Our slicing software continues to evolve, offering better performance and more user-friendly features.
Looking Forward
Formnext SOUTH CHINA 2024 was a remarkable platform for Piocreat to connect with industry leaders, professionals, and enthusiasts. We are proud of the progress we’ve made and are excited to continue pushing the boundaries of 3D printing technology. Thank you to everyone who visited our booth and made this event such a success!
Stay tuned for more exciting developments from Piocreat as we continue to innovate and lead in the world of 3D printing.
For more information about our products and upcoming events, visit our website www.piocreat3d.com. Let’s shape the future of 3D printing together!