Highlights from PioCreat at Fakuma 2024
piocreat3d
on
October 21, 2024
PioCreat 3D proudly participated in Fakuma 2024, one of the world’s premier trade fairs for industrial plastics processing. Held from October 15th to 19th, 2024, at Messe Friedrichshafen, Fakuma brought together 1,636 exhibitors from around the globe, offering attendees a comprehensive look into the latest advancements in plastic technologies. This year’s event focused heavily on efficiency and sustainability, with innovations aimed at reducing environmental impact while improving industrial performance.
At Fakuma 2024, PioCreat stood out by highlighting our cutting-edge Fused Granulate Fabrication (FGF) 3D printing solutions, which emphasize eco-friendly and cost-efficient additive manufacturing. Here’s a look at some of the exciting developments and innovations we showcased during the event.
PioCreat’s Sustainable 3D Printing Solutions
At PioCreat, we are committed to advancing 3D printing technology in ways that not only enhance production capabilities but also contribute to a more sustainable future. Our FGF 3D printing technology, which utilizes plastic pellets and recycled shredded plastic, represents a leap forward in sustainable additive manufacturing.
FGF technology reduces reliance on traditional filament materials by using thermoplastic pellets as feedstock. This process enables faster production while cutting down on material waste and cost. By incorporating recycled plastics, we provide our customers with an environmentally responsible manufacturing solution that doesn’t compromise on quality or performance. This approach is particularly valuable for industries looking to meet growing demands for eco-friendly and sustainable manufacturing practices.
PioCreat Booth at Fakuma 2024: A Hub of Innovation
At our booth located in HALL FO-09, visitors had the opportunity to see our latest innovations in action. Our 3D printers attracted considerable attention, particularly the G5Ultra and the G12 FGF 3D printers, each designed to meet diverse industry needs, from small-scale prototyping to large-scale industrial manufacturing.
The G5Ultra Pellet 3D Printer: A Versatile Solution for Education and Design
The G5Ultra desktop 3D printer became one of the highlights of our booth, generating substantial interest from attendees. We demonstrated the printer’s exceptional capabilities through a live demonstration, during which we printed an exquisite vase on-site. The intricate design and high-quality finish of the vase illustrated the precision and performance that the G5Ultra can achieve, even for complex shapes and delicate structures.
With a built volume of 500×500×400mm, the G5Ultra is designed to cater to various fields, including educational institutions, design studios, prototyping labs, and more. Its cost-effective thermoplastic pellet feedstock enables high-speed production without sacrificing material quality. Key features of the G5Ultra include:
- Nozzle temperature up to 420℃, allowing for a wide range of thermoplastic materials.
- Rapid hot bed heating up to 120℃, ensuring quick setup and print readiness.
- Screw extruder design, providing material flexibility and consistent high-quality output.
This printer is particularly suited for research, design, and academic purposes, where users require precise, repeatable results with the flexibility to experiment with different materials.
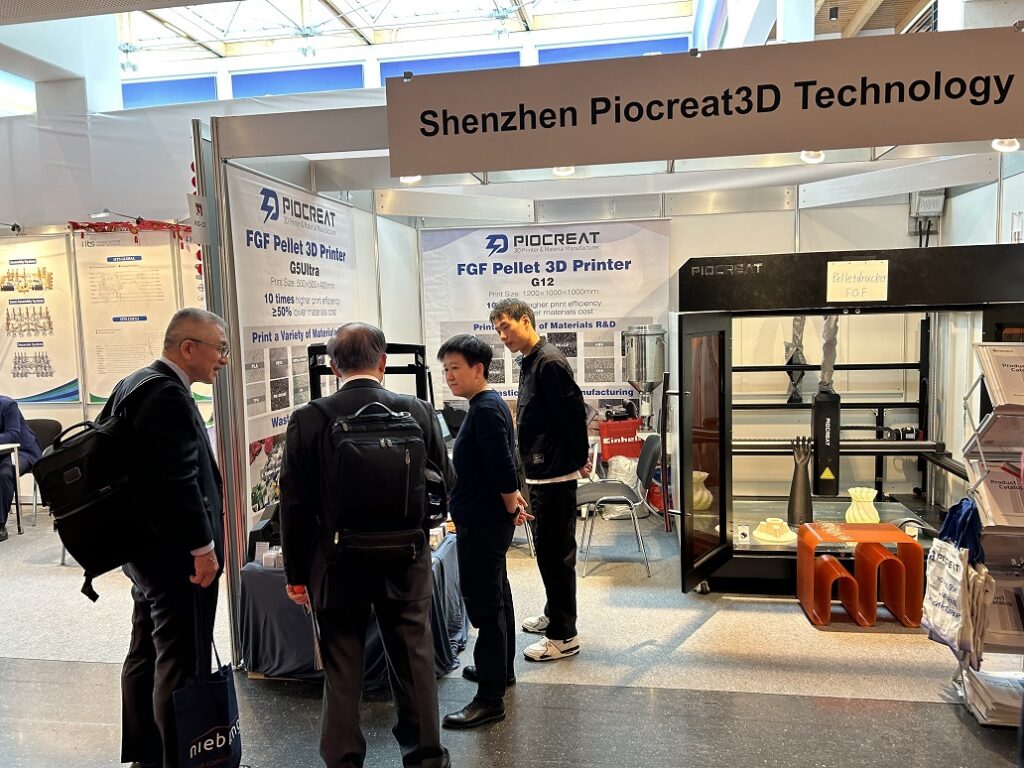
The G12 FGF 3D Printer: Large-Scale Manufacturing at Its Best
Also drawing significant attention was the G12 FGF Pellet 3D Printer, our large-format 3D printing solution. With a built volume of 1200×1000×1000mm, the G12 is perfect for industrial-scale production of large patterns, molds, tooling, jigs, and even full-scale prototypes.
The G12’s ability to produce large parts at high speed is transforming industries such as manufacturing, automotive, aerospace, art, and furniture design. Its Fused Granulate Fabrication process enables the efficient production of sizable objects while maintaining superior material strength and quality. The flexibility to use a wide range of thermoplastic materials, including recycled plastic, makes the G12 a valuable tool for companies seeking to minimize waste and reduce production costs.
Visitors to our booth were impressed by the high-speed thermoplastic extrusion capabilities of the G12, as well as its versatility in creating complex designs for a wide variety of applications.
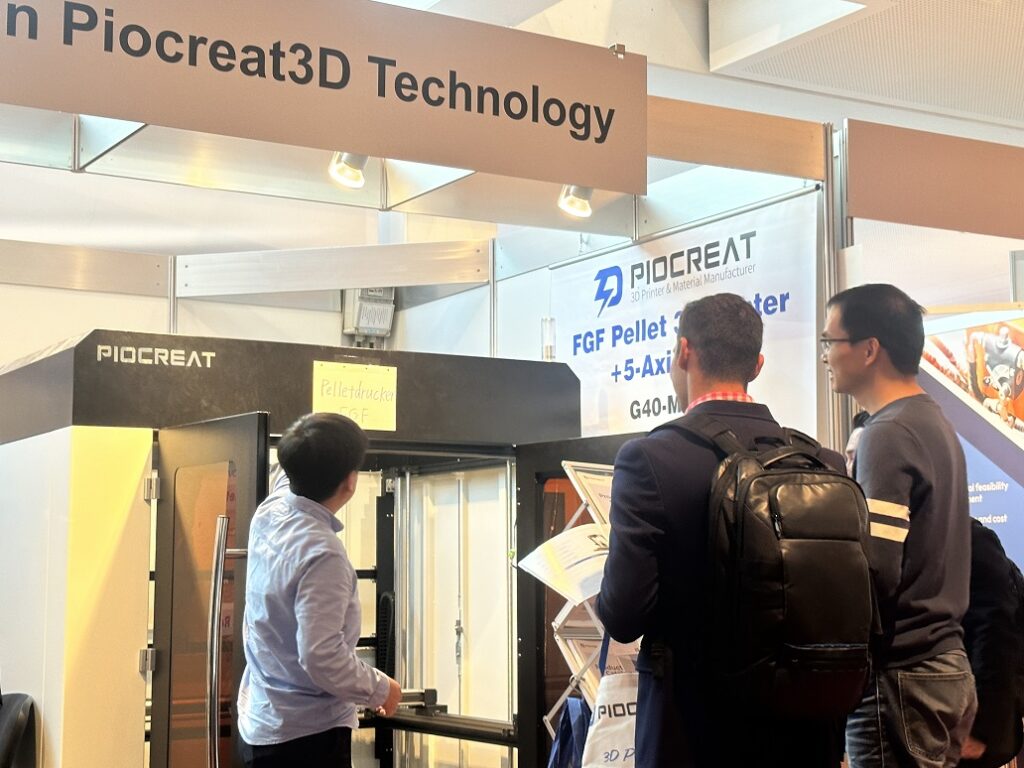
Partnership with Danquinsa GmbH
In addition to our own booth, we were thrilled to see our G5Ultra Pellet 3D Printer showcased at the booth of our partner, Danquinsa GmbH. Danquinsa, a leading provider of TPU solutions, demonstrated how our G5Ultra printer can work seamlessly with their cutting-edge materials, emphasizing both companies’ shared commitment to innovation and sustainability in plastics processing.
By combining Danquinsa’s advanced TPU solutions with the G5Ultra’s robust capabilities, we showcased a new level of material versatility and performance that is particularly well-suited for demanding industrial applications.
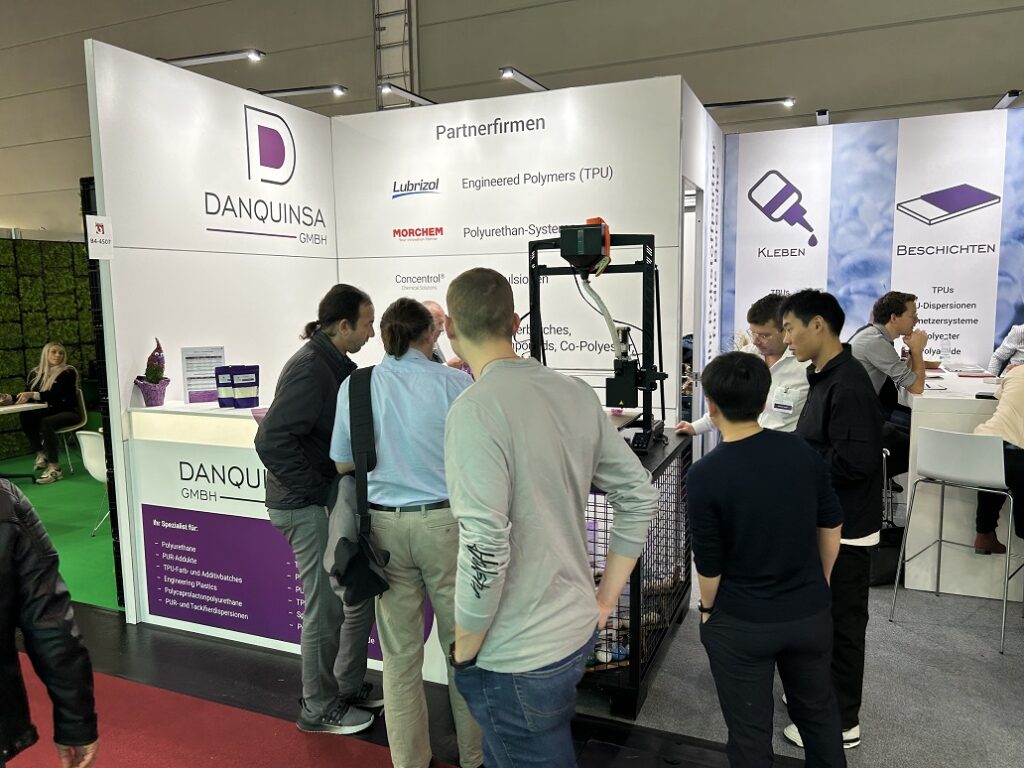
Thank You to Our Visitors
We would like to extend a heartfelt thank you to everyone who visited our booth at Fakuma 2024. Your interest and enthusiasm in exploring the latest innovations in 3D printing technology were deeply appreciated. We enjoyed the opportunity to engage with professionals across industries and discuss how our solutions can help address current and future challenges in additive manufacturing and plastics processing.
The feedback and conversations we had at Fakuma were invaluable, and we look forward to continuing to support the development of sustainable and efficient 3D printing solutions.
About PioCreat 3D
Founded in 2015 and based in Shenzhen, China, PioCreat 3D specializes in the production of innovative 3D printers and advanced materials. Our product portfolio includes:
- Industrial-grade pellet 3D printing solutions
- Dental 3D printing solutions
- Professional resin solutions
We cater to a wide range of industries, including automotive, aerospace, manufacturing, marine, education, dentistry, and medical, offering cutting-edge solutions tailored to the needs of both professionals and educational institutions. PioCreat is dedicated to pushing the boundaries of additive manufacturing, with a focus on sustainability, cost-efficiency, and high-quality performance.