Digital Light Processing in 3D Printing: A Comprehensive Guide
piocreat3d
on
November 14, 2024
Table of Contents
Digital Light Processing (DLP) is a 3D printing technology known for its speed, precision, and high-quality finishes. Originally developed as a digital projection method, DLP has become a popular choice for industries that require complex and intricate 3D-printed parts, such as jewelry, dentistry, and audiology. In this blog post, we’ll take a closer look at how DLP works, the materials it uses, its advantages over other 3D printing methods, and some common applications.
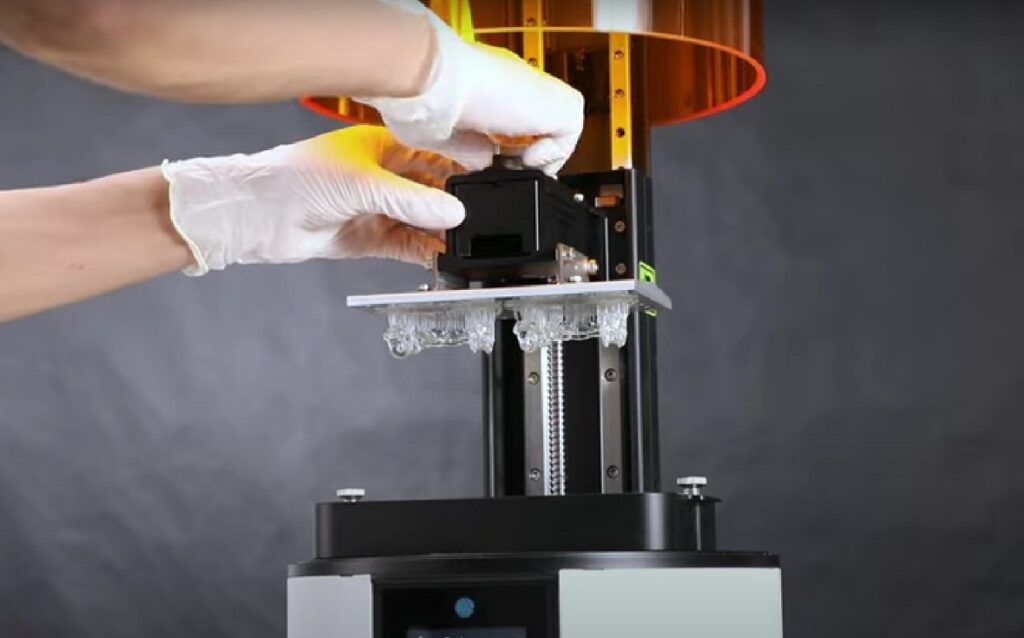
What is Digital Light Processing in 3D Printing?
Digital Light Processing (DLP) is an additive manufacturing process that uses a digital projector to flash layers of UV or visible light onto a liquid photopolymer resin, curing it into a solid shape layer by layer. Unlike Stereolithography (SLA), which uses a laser to trace and cure each layer, DLP uses a projected light source that cures an entire layer simultaneously, significantly reducing production time.
In DLP, the digital projector produces images of each layer based on the 3D model, projecting these images onto the photopolymer resin. When exposed to the projected light, the photosensitive resin hardens, forming the solid structure. By repeating this process layer by layer, a DLP printer can produce intricate and high-quality 3D objects with exceptional accuracy.
How Does Digital Light Processing Work?
DLP technology relies on a UV or visible light projector to cure photosensitive resin into 3D shapes. Here’s how the process works step-by-step:
- Image Projection: The 3D printer’s digital projector flashes an image of a layer onto the resin surface, exposing the resin to light and hardening it into the shape of that layer.
- Layer-by-Layer Curing: After each layer is cured, the printer raises or lowers the build platform, depending on whether the projection is from above or below, and exposes the next layer to light.
- Photopolymerization: The light causes a photopolymerization reaction, turning the liquid resin into a solid layer. This process repeats until the object is fully formed.
- Post-Processing: Once printing is complete, the part may need cleaning, curing, or other post-processing steps to achieve its final finish.
The ability to cure an entire layer at once distinguishes DLP from SLA printing, where each layer is drawn and cured point by point. This simultaneous curing gives DLP a speed advantage, particularly for complex models.
What Materials Are Used in Digital Light Processing?
DLP 3D printing primarily uses photopolymer resins, which are liquid materials that solidify when exposed to UV light. There are several types of resins and materials that can be used in DLP printing:
UV-Curable Resins: These are the most common resins used in DLP, designed to react to UV light. They come in various colors, transparencies, and material properties, from rigid to flexible options.
Thermoplastic Resins: Some specialized DLP printers can use thermoplastic resins, which offer additional durability and strength, making them suitable for engineering applications.
Metal-Infused Resins: Certain DLP printers support resins infused with metal particles, creating parts that resemble metal and are commonly used in industries like jewelry and engineering.
Medical-Grade Resins: These resins are specially formulated to meet the safety and performance requirements for healthcare and dental applications, ensuring biocompatibility.
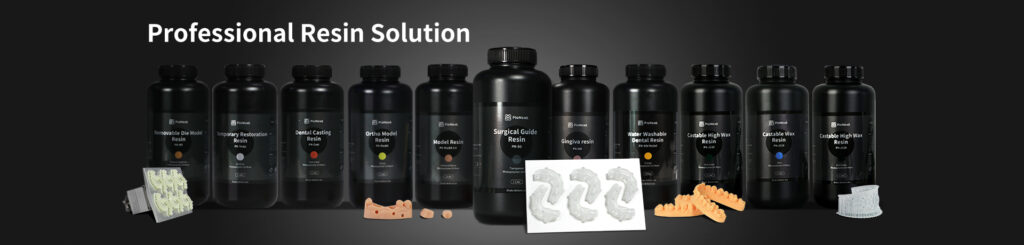
The choice of resin depends on the specific application requirements, such as the need for strength, flexibility, transparency, or biocompatibility.
Advantages of Digital Light Processing
DLP 3D printing offers several advantages that make it ideal for industries requiring high precision, speed, and quality. Here are some key benefits of DLP:
1. High-Quality Surface Finish
DLP printers are known for their ability to create smooth, detailed surfaces. The high resolution and accuracy of DLP printing are ideal for applications like jewelry, dentistry, and other fields where aesthetics and intricate details are essential.
2. Faster Production Times
Since DLP technology cures an entire layer at once, it is generally faster than SLA, which traces each layer point by point. This makes DLP an excellent choice for producing multiple small, intricate parts or large models in a shorter time frame.
3. Cost-Effective for Complex Parts
DLP offers cost savings over some traditional methods, especially for low-volume, high-complexity parts. The quality of DLP-printed components is often comparable to that of conventional manufacturing methods like injection molding, making it a valuable tool for prototyping and small-batch production.
4. High Detail Accuracy
DLP printing offers precise control over each layer, producing parts with exceptional detail and accuracy. This level of control makes it possible to create complex shapes with intricate patterns, ideal for industries like jewelry, audiology, and dental restoration.
DLP vs. Stereolithography (SLA): Key Differences
While both DLP and SLA are photopolymer-based technologies, they differ in several key ways:
Light Source: SLA uses a laser to trace each layer, while DLP uses a projector to cure an entire layer at once. This difference in light source affects both speed and cost.
Production Speed: DLP is generally faster than SLA since it cures an entire layer simultaneously, making it more suitable for larger batches or parts with intricate details.
Resolution and Detail: While both technologies offer high-resolution prints, DLP tends to have a slight edge in speed without sacrificing detail, especially for small and complex designs.
Cost-Effectiveness: DLP’s rapid layer-by-layer curing process often makes it more cost-effective for intricate parts, especially for high-detail and small-scale production.
These differences allow users to choose the technology that best fits their needs, depending on the required level of detail, speed, and budget.
Applications of Digital Light Processing 3D Printing
DLP’s high precision and speed make it versatile for a variety of industries, each benefiting from its unique capabilities.
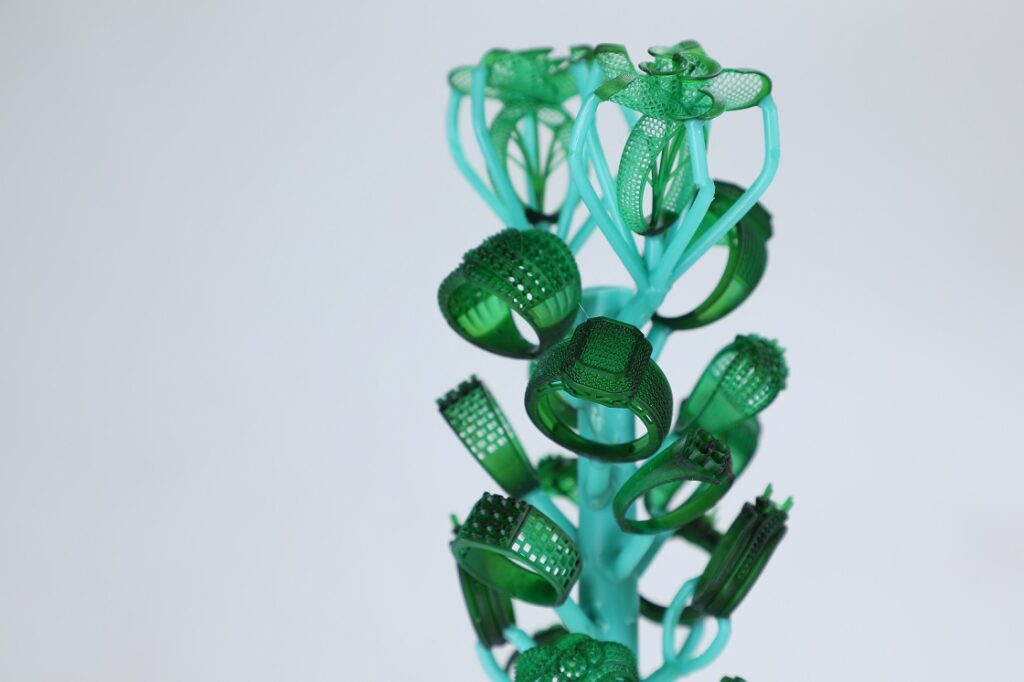
Jewelry Making
DLP printing is widely used in the jewelry industry to create highly detailed patterns and molds for casting. With DLP, jewelers can produce intricate designs with the smooth surface finish and sharp details required for high-quality jewelry, from rings to pendants.
Dentistry and Healthcare
DLP is commonly used in dentistry for creating crowns, bridges, and surgical guides. Its precision ensures that dental models and prosthetics fit accurately, reducing adjustments and improving patient outcomes. Medical-grade resins make DLP a safe option for healthcare applications.
Engineering and Manufacturing
DLP printing is valuable for creating engineering prototypes and small-batch parts that require high strength and durability. Its accuracy makes it ideal for functional testing, allowing engineers to validate designs before mass production.
Audiology
In audiology, DLP printing is used to create custom hearing aids, earmolds, and other audio devices tailored to individual needs. The precision and speed of DLP allow for high-quality parts that meet the comfort and fit requirements of audiology products.
Piocreat DLP 3D Printers: Advanced Solutions for Precision Printing
Piocreat offers a range of high-quality DLP 3D printers tailored to industries that require speed and precision. Here are two standout models:
D158: Compact and Precise
The D158 is a compact DLP 3D printer designed for dental labs, orthodontics, and professional applications requiring high detail. Built with Texas Instruments technology, the D158 provides precision, reliability, and ease of use.
- 62μm Pixel Size: High resolution for detailed prints.
- Automatic Lifting Cover: Protects the print area from dust and environmental interference.
- High-Speed Release Film: Enables faster prints without compromising quality.
- Stable Z-axis Structure: Provides consistency and reliability across prints.
D150: High-Speed Productivity
The D150 is Piocreat’s fastest DLP 3D printer, ideal for high-volume production. With adjustable light intensity and a high-speed release film, the D150 offers unmatched productivity without sacrificing quality.
- Speeds up to 80mm/h: Fast printing speed for high-volume production.
- Adjustable Light Intensity: Customizable settings for different materials.
- Light Engine Life: 30,000+ hours for long-term use.
These Piocreat printers offer professionals in jewelry, dentistry, and other fields the tools they need to produce accurate, high-quality parts efficiently.
Conclusion
Digital Light Processing (DLP) 3D printing is transforming industries by providing a fast, precise, and cost-effective solution for producing complex parts. With applications ranging from jewelry and dentistry to engineering, DLP offers unique advantages in speed, surface quality, and detail accuracy. Piocreat’s DLP printers, like the D158 and D150, are designed to meet the needs of professionals in various industries, offering high productivity and precision.
As 3D printing technology continues to advance, DLP remains a vital tool for those who need high-quality prints and rapid turnaround times. Whether you’re a jeweler creating intricate designs or a dental lab crafting custom-fit models, DLP offers a versatile, reliable solution for your 3D printing needs.