3D Printed Art Decoration for Museum – A Collaboration Between Samaya Investment and PioCreat
piocreat3d
on
May 22, 2025
In the evolving landscape of museum and exhibition design, innovation, artistry, and sustainability must work in harmony. This vision recently came to life through a remarkable collaboration between Samaya Investment, a Saudi company specializing in cultural and exhibition projects, and PioCreat, a leader in industrial 3D printing technology.
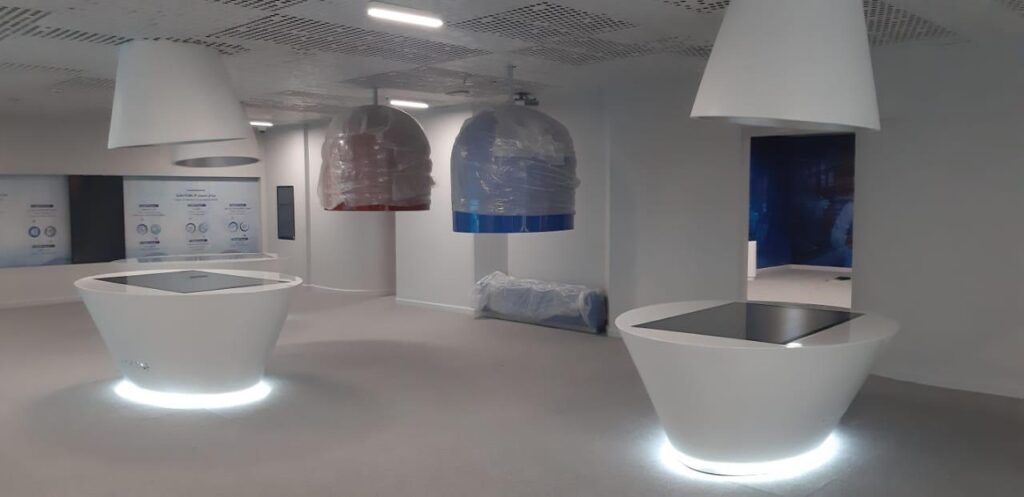
The Vision Behind the Project
Samaya Investment is renowned for delivering world-class cultural experiences, offering services that span architectural design, interior planning, and technical development for museums, visitor centers, and exhibitions—both permanent and temporary. Their team is committed to transforming narratives into immersive physical spaces that engage, educate, and inspire.
In one of their latest museum projects, Samaya aimed to integrate large-scale artistic installations that not only stood out visually but also aligned with sustainable and innovative production methods. For this purpose, they turned to PioCreat and its cutting-edge G12 FGF (Fused Granulate Fabrication) Pellet 3D Printer.
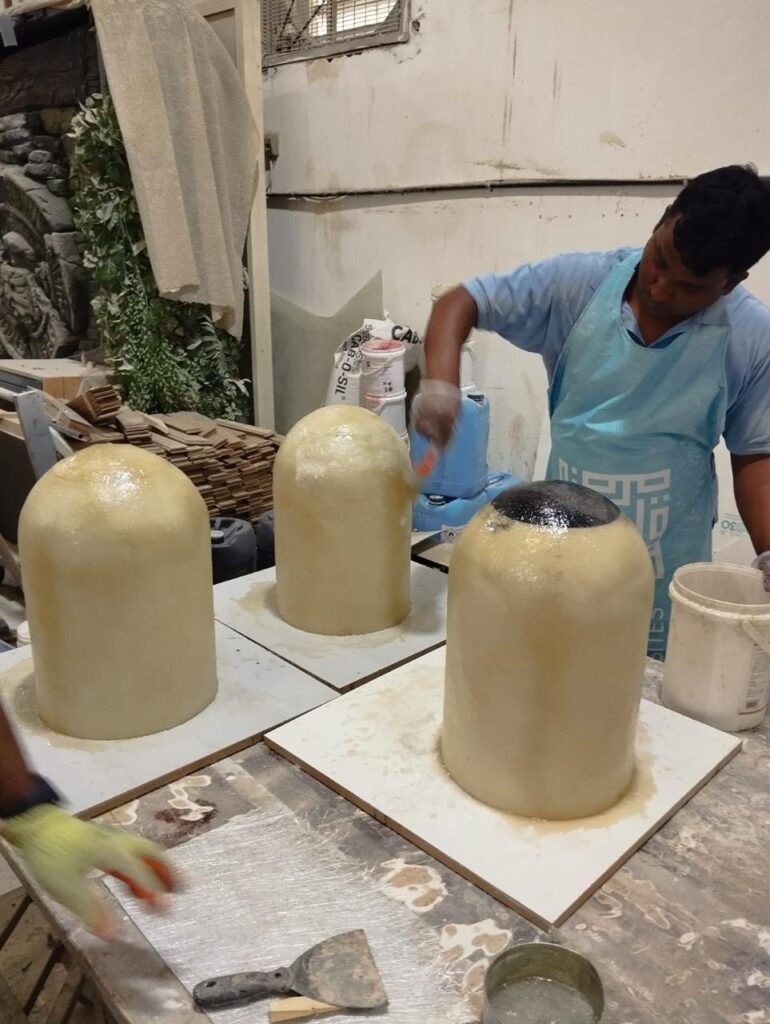
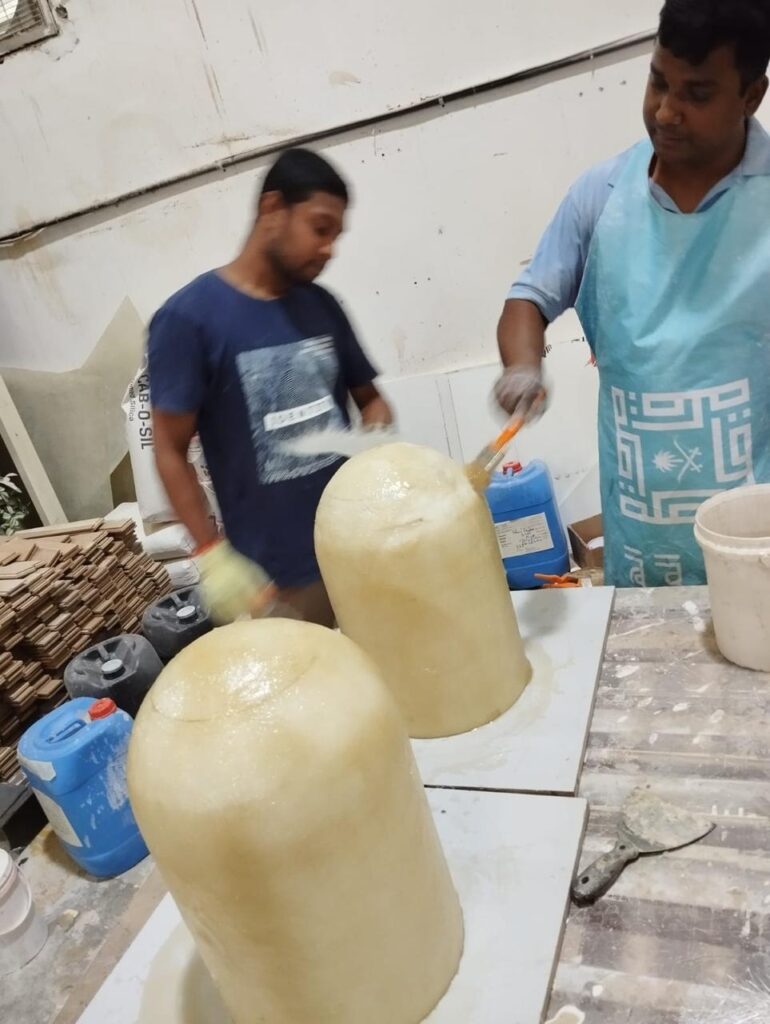
Why the PioCreat G12 Was the Perfect Fit
For this ambitious project, the G12 offered a number of decisive advantages:
Speed to Market: The G12 enabled rapid prototyping and full-scale production of large decorative elements in a fraction of the time required by traditional fabrication methods. This agility allowed Samaya’s design team to swiftly iterate and gain client approvals without delays.
Cost Efficiency: Using thermoplastic pellets, the G12 bypassed the need for costly molds and tooling. This digital-to-physical workflow significantly reduced production costs and improved overall budget control.
Design Freedom: The G12’s ability to print large, complex geometries gave Samaya the freedom to explore organic forms, intricate textures, and bold structures that would be difficult or impossible to achieve with conventional manufacturing.
Sustainable Innovation: With minimal waste and the use of recyclable ABS material, the project embraced eco-conscious practices—a key value for both Samaya and the cultural institutions they serve.
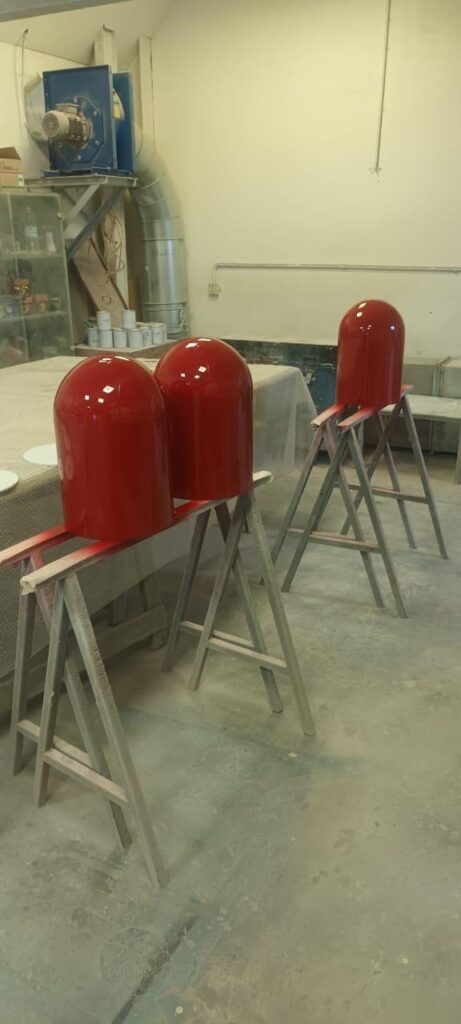
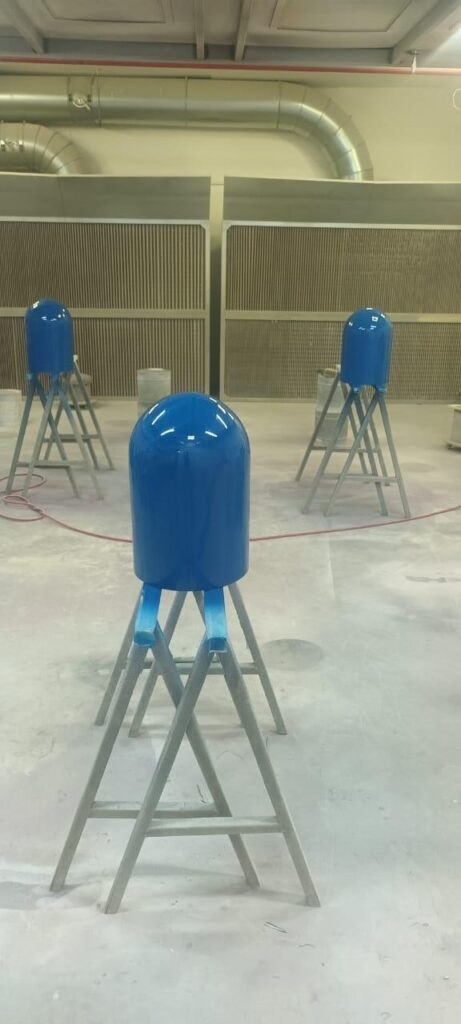
Bringing the Installation to Life
The final product was a series of large-format, visually captivating art installations that became focal points within the museum’s new exhibit space. Printed in durable ABS using the G12 and then finished with custom painting and surface treatments, the results were stunning—vivid in color, intricate in form, and seamless in execution.
These installations not only enhanced the visual narrative of the museum but also demonstrated the practical power of additive manufacturing in architectural and cultural design applications. Compared to traditional sculpting or fabrication techniques, the G12 dramatically improved production speed and reduced logistical complexities.
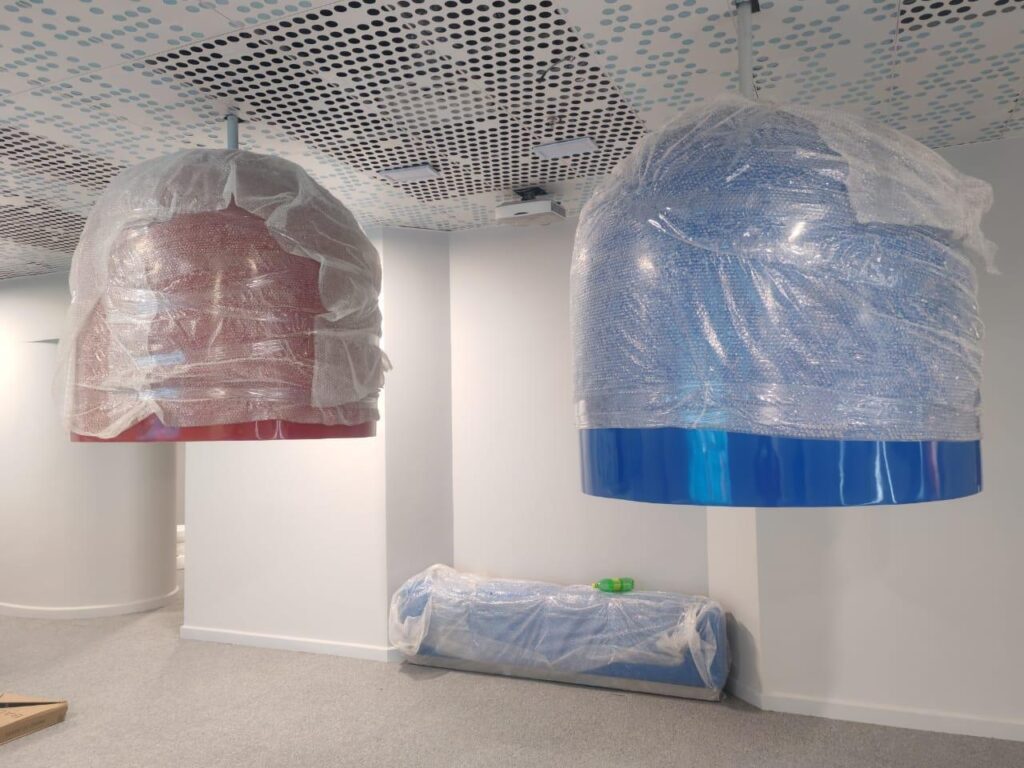
A New Era for Exhibition Design
This collaboration between Samaya Investment and PioCreat showcases a broader shift in how designers, curators, and fabricators are approaching modern exhibition and museum planning. Additive manufacturing is no longer just a prototyping tool; it is becoming a core enabler of artistic expression, operational efficiency, and sustainable design in the cultural sector.
“With the G12, we were able to turn bold artistic visions into tangible centerpieces in record time, while staying true to our commitment to quality and sustainability,” said a Samaya project representative. “It’s not just technology—it’s a tool for storytelling.”
About the PioCreat G12
The G12 Pellet 3D Printer is designed for large-format, high-speed extrusion using open-source thermoplastic pellets. Ideal for manufacturing patterns, molds, artistic structures, tooling, and full-scale prototypes, it supports a wide range of materials and is equipped for demanding creative and industrial environments.