3D Printing Dental Implants: Transforming the Dental Industry
piocreat3d
on
April 12, 2024
3D printing dental implants is transforming the dental industry by enhancing precision, efficiency, and patient outcomes. As dental professionals increasingly adopt 3D printing technology, they are able to produce highly accurate and customized dental implants. This article delves into the specifics of 3D printed dental implants, exploring their benefits, materials used, and the best 3D printers for this application.
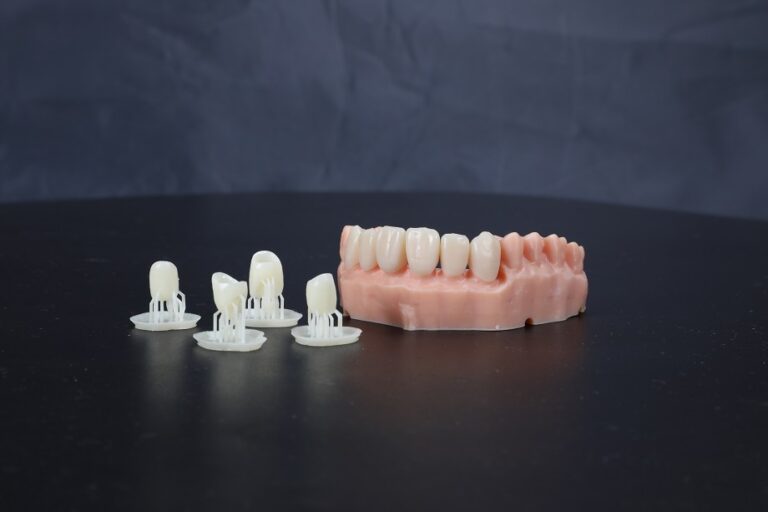
What is a 3D Dental Implant?
A 3D dental implant is a custom-made tooth replacement produced using advanced 3D printing technology. Unlike traditional dental implants, which involve multiple steps and manual crafting, 3D printed implants are designed digitally and manufactured layer by layer using a 3D printer. This process allows for greater customization and precision, ensuring that the implant fits perfectly into the patient’s jawbone.
3D dental implants typically consist of two main components: the implant body, which is inserted into the jawbone, and the abutment, which connects the implant to the dental prosthesis (crown, bridge, or denture). The digital workflow begins with capturing detailed scans of the patient’s oral cavity using intraoral scanners. These scans are then used to create a digital model of the implant, which is sent to a 3D printer for fabrication.
Can You 3D Print Dental Implants?
Yes, you can 3D print dental implants. The process of 3D printing dental implants involves using specialized materials and printers that can produce highly detailed and accurate dental components. Dental professionals use computer-aided design (CAD) software to design the implant based on the patient’s specific anatomical features. The digital design is then printed using a 3D printer, layer by layer, until the final implant is created.
3D printing technology allows for the creation of implants that are tailored to each patient’s unique needs. This customization ensures a better fit and reduces the likelihood of complications. Additionally, 3D printing can produce complex geometries that are difficult or impossible to achieve with traditional manufacturing methods. This capability is particularly beneficial for creating intricate dental implants that mimic the natural structure of teeth and bone.
What Materials Are Used for 3D Printed Dental Implants?
The materials used for 3D printed dental implants must be biocompatible, durable, and capable of withstanding the forces of chewing. One of the most commonly used materials for 3D printed dental implants is Surgical Guide Resin. This material is a transparent, Class I biocompatible resin designed specifically for crafting surgical guides and dental implants.
Surgical Guide Resin offers several advantages:
- Biocompatibility: Safe for use in the human body, reducing the risk of adverse reactions.
- Transparency: Allows for clear visibility during surgical procedures, facilitating accurate placement.
- High Precision: Ensures exceptional accuracy and performance, critical for implant-guided procedures.
- Durability: Provides excellent pressure and impact resistance, ensuring the longevity of the implants.
In addition to Surgical Guide Resin, other materials such as titanium and zirconia are also used for 3D printed dental implants. These materials are known for their strength, biocompatibility, and ability to integrate well with the jawbone.
Benefits of 3D Printed Implants
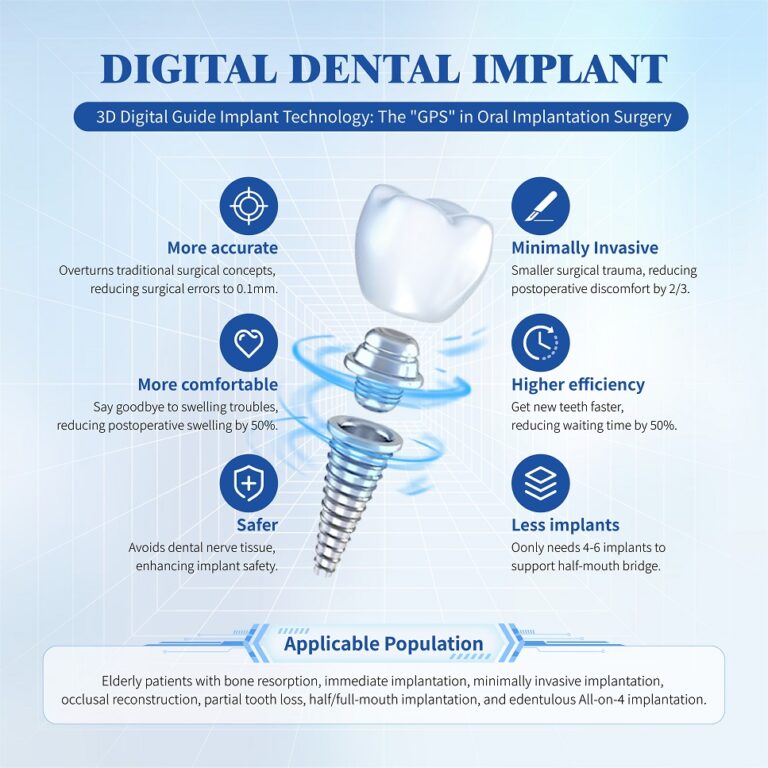
Speed
One of the most significant advantages of 3D printing dental implants is the rapid production time. Traditional methods can take several weeks, involving multiple steps and patient visits. In contrast, 3D printing allows for the quick creation of dental implants, often within a few hours, significantly reducing treatment time.
Precision
3D printing technology ensures a high level of precision in the creation of dental implants. The digital design process allows for meticulous planning and customization, resulting in implants that fit perfectly and function optimally. This precision reduces the need for adjustments and improves the overall success rate of the implants.
Cost-Effectiveness
By streamlining the production process and reducing the need for manual labor, 3D printing makes dental implants more affordable. This cost-effectiveness benefits both dental practices and patients, making high-quality dental care more accessible.
Customization
3D printing enables the production of highly customized dental implants tailored to each patient’s unique anatomy. This customization enhances the comfort and effectiveness of the implants, leading to better patient outcomes.
3D Printers Used for Dental Implants
Choosing the right 3D printer is crucial for achieving optimal results in dental implant production. Piocreat offers top-of-the-line 3D printers designed for the dental industry. Two standout models are:
DJ89 PLUS 8K 10.3″ LCD 3D Printer
- Top cost-effective resin 3D printer for dental industries
- 29μm Pixel Size: Delivers unmatched print clarity and detail, ensuring precise reproduction of the implant design.
- Heating Chamber: Ensures consistent temperature for optimal printing conditions, maintaining the quality of the printed implants.
- Automatic Feeding: Simplifies the printing process and reduces manual intervention, enhancing efficiency.
- Stable Z-axis Structure: Provides precise and reliable prints, crucial for producing high-quality dental implants.
- Texas Instruments Technology: Utilizes advanced technology for precision and reliability.
- Automatic Lifting Cover: Enhances usability and simplifies the printing process.
- 62μm Pixel Size: Offers high-resolution prints, ensuring detailed and accurate dental implants.
- High Speed Release Film: Improves printing efficiency by reducing the time required for layer separation.
- Stable Z-axis Structure: Ensures consistent and precise printing, essential for dental applications.
Both models are designed to meet the demanding requirements of dental professionals, providing the accuracy and reliability needed for successful implant procedures.
Wrapping Up
3D printing dental implants is revolutionizing the dental industry by offering unparalleled precision, efficiency, and customization. By utilizing advanced 3D printing technology and high-quality materials like Surgical Guide Resin, dental professionals can produce custom implants quickly and accurately. With dental 3D printers like the DJ89 PLUS and D158, the future of dental implantology is brighter and more efficient than ever.
The adoption of 3D printing in dental implant production not only enhances the quality of care but also streamlines workflows, making dental practices more productive and effective. As the technology continues to evolve, we can expect even greater advancements in the field of dental implants, leading to improved patient outcomes and satisfaction.