PioCreat & PioNext to Attend LMT LAB DAY Chicago 2025
piocreat3d
on
January 15, 2025
We’re excited to announce that PioCreat & PioNext will be participating in the 40th Annual LMT LAB DAY Chicago 2025, the world’s largest dental laboratory event! From February 20 to 22, we’ll be at Booth B-2, East Exhibit Hall, Hyatt Regency Chicago, showcasing our latest cutting-edge dental 3D printing innovations.
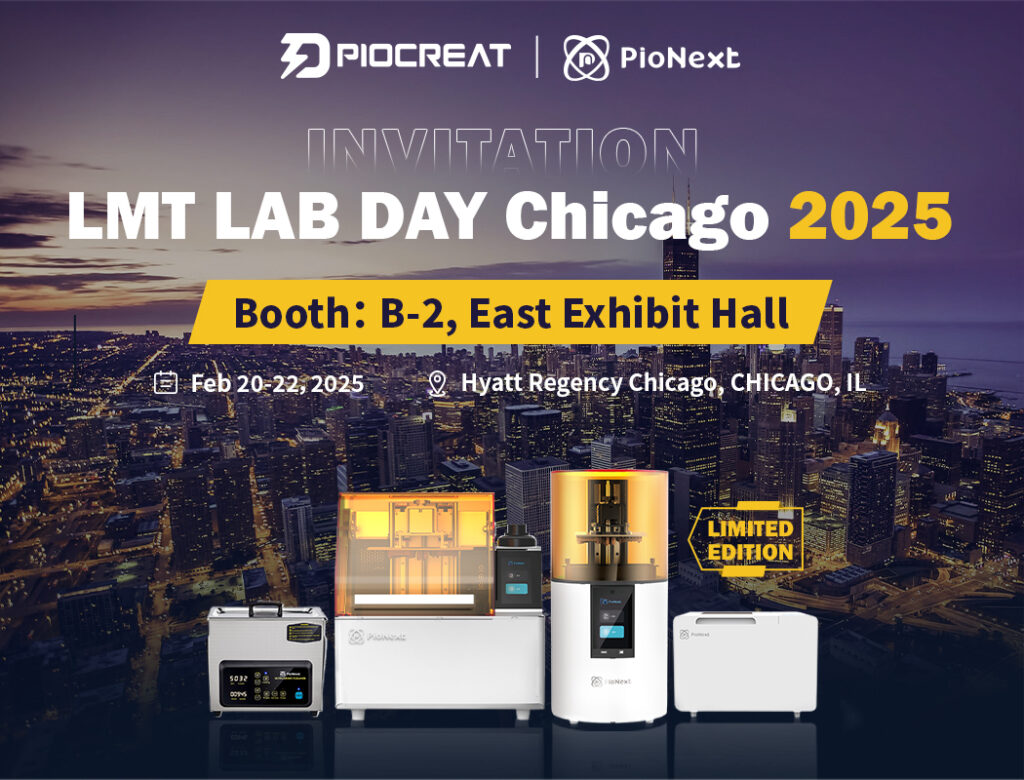
About LMT LAB DAY Chicago 2025
Celebrating its 40th anniversary, LMT LAB DAY Chicago is the premier annual gathering for the global dental laboratory community. Since its inception in 1985, this event has grown exponentially, with over 275 exhibitors, two expansive exhibit halls, more than 4,600 attendees, and a packed schedule of engaging seminars.
The event offers a unique opportunity for dental professionals, lab technicians, and industry experts to explore new technologies, learn from seasoned speakers, and network with peers. It’s the perfect platform for PioCreat & PioNext to demonstrate how our innovative solutions are shaping the future of digital dentistry.
PioNext: Your One-Stop Dental 3D Printing Solution
PioNext, a dedicated sub-brand of PioCreat, focuses exclusively on the research, development, and production of high-quality dental equipment and consumables. We offer one-stop professional digital dental solutions, combining advanced 3D printing technology, specialized dental resins, and essential post-processing tools. Whether you’re a dental lab, orthodontist, or dentist, PioNext provides the perfect solution for creating customized, precise dental appliances with ease.
Exclusive One-Stop Package Deals at LMT LAB DAY Chicago
To celebrate our presence at LMT LAB DAY Chicago, we’re thrilled to offer limited-time, exclusive package deals that deliver unbeatable value:
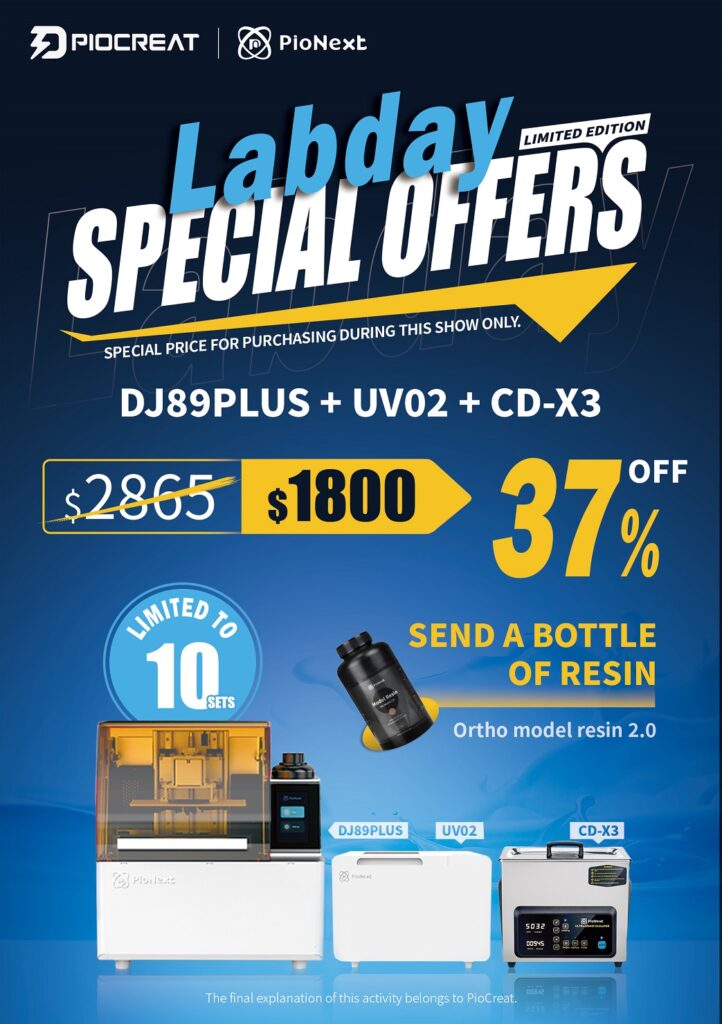
Package 1 – DJ89PLUS + UV02 + CD-X3
Enjoy 37% off on this complete solution for dental professionals. This package includes the DJ89PLUS 3D printer, UV02 curing machine, and CD-X3 washing unit—everything you need for fast, accurate, and high-quality dental appliance production.
Package 2 – D158 + UV02 + CD-X3
Take advantage of an incredible 55% discount on our advanced D158 3D printer bundle, designed for high-precision dental printing. Paired with the UV02 and CD-X3, this package offers exceptional performance at a significantly reduced price.
These packages are ideal for dental professionals looking to upgrade their equipment, enhance productivity, and improve patient outcomes with cutting-edge technology.
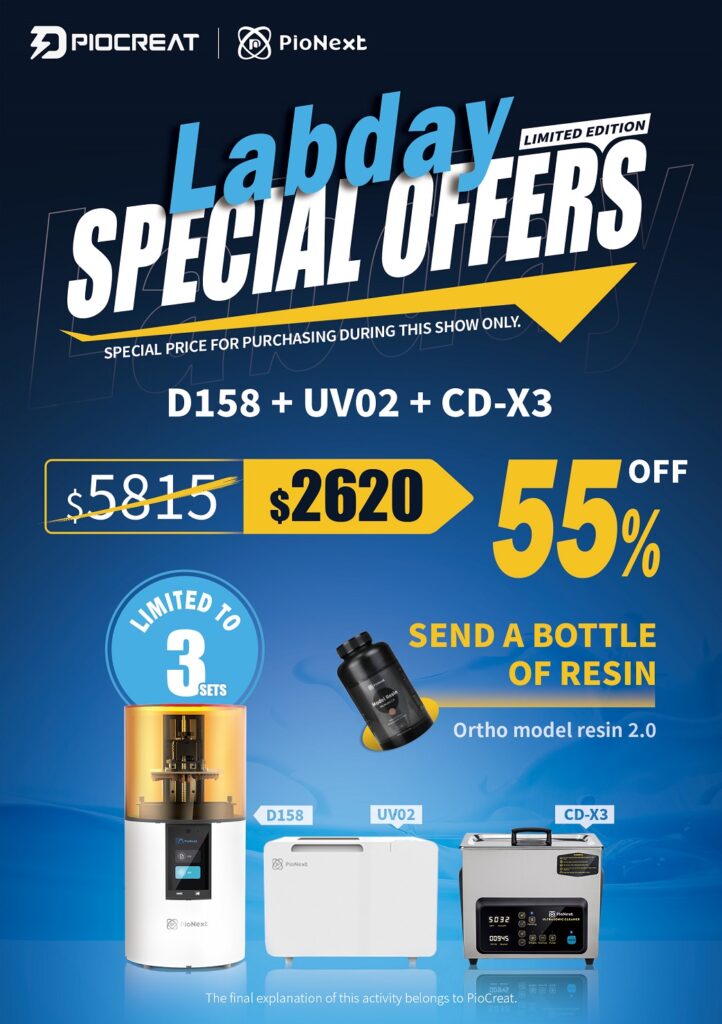
A Partnership for Progress
This exclusive promotion is part of our strategy to expand brand awareness and penetrate new markets. We’re inviting customers who purchase our products during the event to provide objective reviews, feedback, and suggestions. Your insights will help us refine our offerings and ensure that we continue to meet the evolving needs of dental professionals.
Mark your calendars for LMT LAB DAY Chicago 2025 and join us for an unforgettable experience. Together, let’s explore new possibilities in digital dentistry!
For more information, visit our website or follow us on LinkedIn for the latest updates.
See you in Chicago!