Marine and boat manufacturing has long been reliant on traditional, costly methods that are time-consuming and wasteful. 3D printing, also known as additive manufacturing, is now making waves in this sector, offering significant advantages in terms of time, cost, and customization. From creating large-scale boat molds to producing complex yacht components, this technology is transforming the way we build and maintain vessels, big and small.
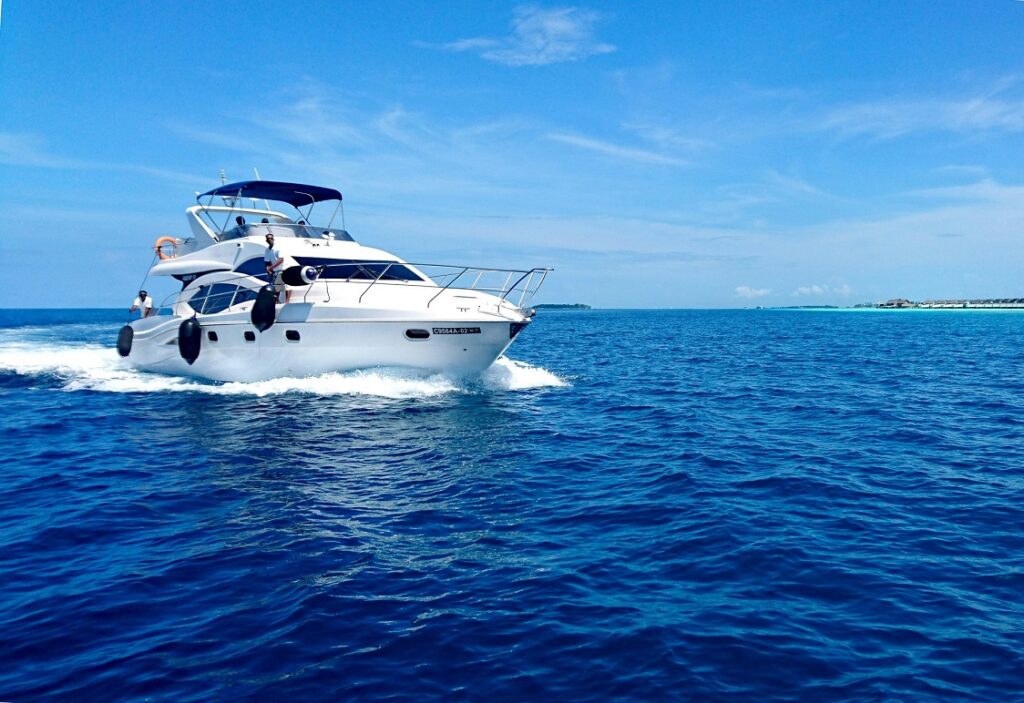
Conventional Challenges in Marine Manufacturing
Boat manufacturing has historically been a labor-intensive process. Building a custom boat or yacht often requires creating a master mold, a process that can take several weeks and demand high precision. Materials like plywood, stainless steel, and plastics are shaped through subtractive processes like CNC milling, generating a great deal of waste. These methods pose limitations when it comes to producing intricate, geometrically complex parts, leading to higher costs and extended downtimes.
For large ships, maintenance can be equally time-consuming. Components may need to be custom-made, adding to downtime and repair costs. Traditional methods simply don’t offer the flexibility and speed required in today’s fast-paced maritime environment.
Is it Possible to 3D Print a Boat?
Yes, it is absolutely possible to 3D print a boat. Thanks to advancements in large-format 3D printing, manufacturers can now produce everything from boat parts to full hulls. By printing directly with thermoplastics, composite materials, and even recycled materials, companies can create durable and functional boats while minimizing waste.
For example, companies like Tanaruz have already begun 3D printing entire boats using polymer-based materials, offering a sustainable alternative to traditional boat manufacturing methods.
Are Rafts Worth 3D Printing?
While 3D printing smaller marine components like rafts may not have the same dramatic impact as printing larger parts like hulls, it is still a worthwhile endeavor. Rafts and other smaller watercraft components can be produced rapidly, with the option to customize designs based on specific needs. This reduces both production time and material waste, while allowing manufacturers to offer highly personalized products to customers.
Applications of 3D Printing in Marine Manufacturing
3D printing presents a much-needed alternative. By using additive manufacturing, boat and yacht manufacturers can create parts layer by layer, optimizing materials and reducing waste. Moreover, the ability to produce complex geometries and customized designs with ease opens up new possibilities for maritime engineering.
Some of the most prominent applications of 3D printing in marine manufacturing include:
Customized End-Use Parts: These include fins, masts, radar antennas, dashboards, rooves, and hull extensions. 3D printing allows for the rapid production of these components, tailored to the specific needs of the vessel.
Interior Fixtures: Bathrooms, sinks, and other design elements can be directly 3D-printed, offering both aesthetic and functional flexibility.
Directly-Printed Large Molds: Traditional boat molds can now be printed, reducing the need for extensive manual labor and material waste.
Full-Scale Prototypes: 3D printing offers an ideal solution for developing full-scale prototypes, which can be used to test designs before committing to full production.
Advantages of 3D Printing in Marine Manufacturing
The benefits of 3D printing for boat manufacturing are significant, particularly when compared to traditional methods:
1. Cost-Efficient Production
The production of large-scale custom parts no longer requires costly molds and long lead times. 3D printing can create complex components directly from digital designs, reducing both the cost of materials and the time needed for production.
2. Reduced Waste
Traditional methods of shaping materials often lead to substantial waste. Additive manufacturing, by contrast, uses only the material necessary for the build, cutting down on scrap and making the process far more sustainable.
3. Faster Turnaround
With 3D printing, it’s possible to create marine parts within hours rather than weeks. For instance, yacht components like masts, fins, and hulls can be produced rapidly, enabling quicker repairs and less time spent out of the water.
4. Specialized Materials for Harsh Conditions
Marine environments are demanding, and components must withstand salt water, extreme weather, and constant wear and tear. 3D printing technologies now use advanced thermoset materials that are optimized for durability. Fiber-reinforced plastics and recycled alternatives are increasingly being used to manufacture parts that resist corrosion and remain reliable over time.
5. Part Optimization and Design Freedom
3D printing enables designers to create complex parts that are optimized for both weight and performance. Large assemblies that once required multiple components can now be consolidated into single, seamless parts. This reduces the number of assembly steps and enhances structural integrity, especially for geometrically complex pieces.
6. Sustainable Manufacturing
One of the most exciting aspects of 3D printing in boat manufacturing is its potential for sustainability. By using recycled and upcycled materials, and eliminating the need for molds, manufacturers can significantly reduce their environmental footprint. This is particularly important for industries like boat building, which traditionally consumes vast amounts of resources and energy.
Examples of 3D Printing in Marine Manufacturing
Several companies have already demonstrated the remarkable potential of 3D printing in marine environments. Here are a few noteworthy examples:
1. Tanaruz Boats: A Sustainable Approach
Tanaruz, a Dutch company, focuses on sustainability by producing 3D-printed boats from recycled polymers. Their boats, designed with a circular economy in mind, can be shredded and re-used once they reach the end of their life cycle. Customers can customize their boats through an app, choosing from several models that can then be printed to their specifications. These boats not only save time and energy but also reduce environmental impact, aligning with Tanaruz’s commitment to sustainable manufacturing.
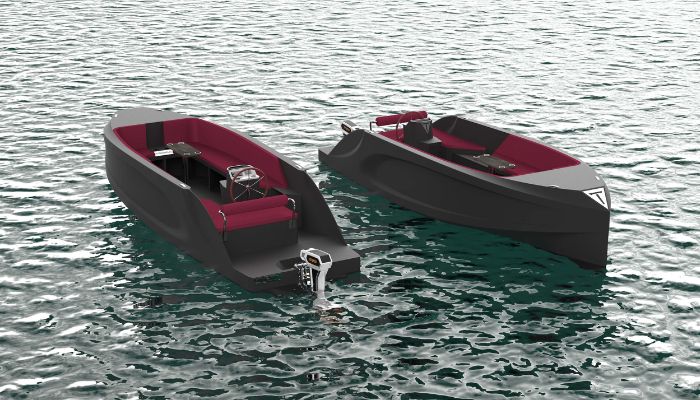
(Image Credit: Tanaruz)
2. The Autonomous Ferry for the 2024 Olympic Games
A collaboration between Holland Shipyards Group, Sequana Développement, and Roboat is bringing an ambitious project to life—a 3D-printed autonomous ferry. This vessel, designed for use during the 2024 Paris Olympic Games, will help alleviate road congestion while minimizing CO2 emissions. Built using recycled materials, it represents the largest 3D-printed autonomous ferry in the world. The project demonstrates how 3D printing can be applied to large-scale, cutting-edge marine solutions.
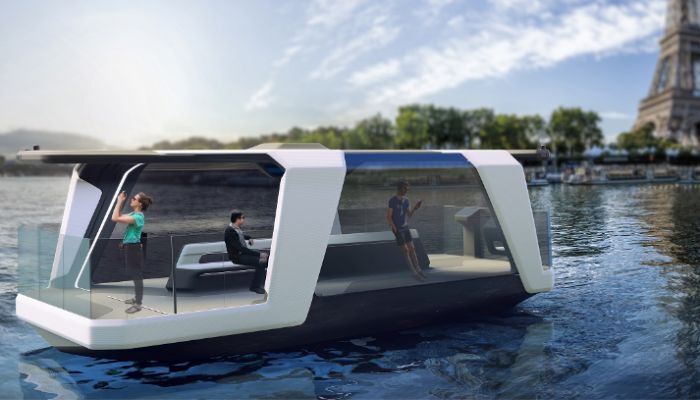
(Image Credit: Roboat)
3. Piocreat’s Advanced 3D Printed Yacht Components
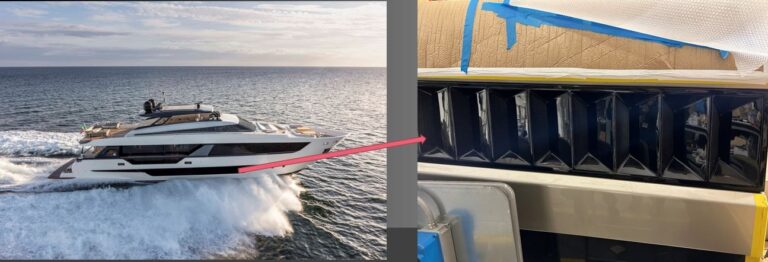
Piocreat’s additive manufacturing systems have been used to print full-scale marine components on-demand. Their use of ASA pellets in their G40 pellet printer has proven ideal for creating resilient and durable yacht parts. These components are specifically designed to endure the harsh marine environment, showcasing how 3D printing can improve both the performance and lifespan of maritime vessels.
The Future of 3D Printing in Marine Manufacturing
As 3D printing continues to evolve, it is expected to play an even more significant role in marine and boat manufacturing. The ability to produce large, customized parts quickly and sustainably makes it an attractive option for manufacturers and boat owners alike. With advancements in materials science, it’s likely that 3D-printed boats and components will become even more durable and versatile, further reducing costs and environmental impact.
The marine industry is just beginning to tap into the full potential of additive manufacturing, but the early results are already promising. Whether it’s a small custom yacht or a large-scale ferry, 3D printing offers a future where boats can be made faster, cheaper, and with far greater design freedom than ever before.