Table of Contents
3D printed molds are transforming the manufacturing industry, providing a flexible, time- and cost-effective alternative to traditional mold-making methods. For companies involved in thermoforming and manufacturing large plastic components, the integration of 3D printing technology offers a solution to the pressures of speeding up production, reducing waste, and cutting costs. In this blog, we will explore the benefits of 3D printing large plastic molds, the materials used, and the best 3D printers for creating these molds.
Overview
Thermoforming manufacturers that use thermoformed components in their production processes are facing severe pressure to speed up production, reduce waste, and bring down costs, all while dealing with a shortage of specialized labor. FGF 3D printing technology can deliver high-performance plastic molds that produce quality parts while drastically reducing lead times and labor costs compared to traditional methods. Piocreat 3D offers innovative 3D printing solutions for large molds used in thermoforming heavy gauge plastics.
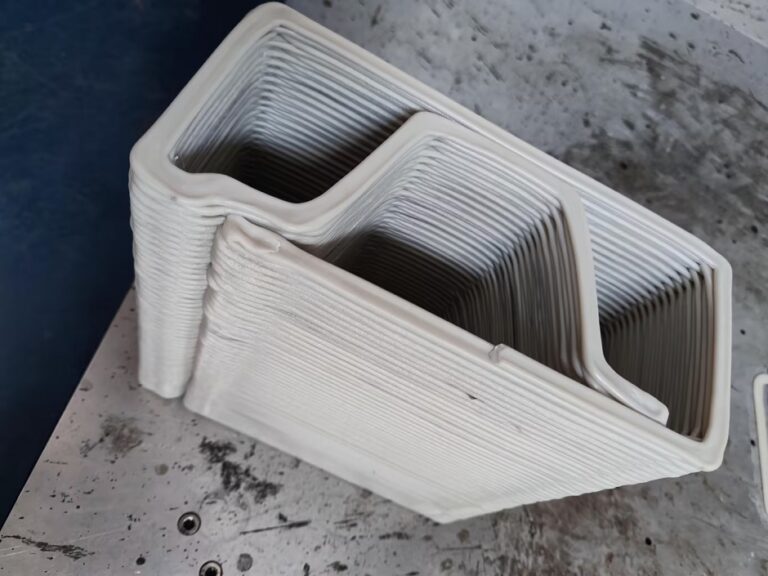
Benefits of 3D Printing Large Plastic Molds
3D printing molds offer several advantages over traditional mold-making methods:
Fast Validation
One of the primary benefits of 3D printing molds is the ability to quickly validate designs. Traditional mold-making processes can be time-consuming, often requiring several iterations before a final mold is approved. With 3D printing, manufacturers can rapidly produce prototypes and make necessary adjustments, ensuring the final mold meets all specifications. This rapid validation process helps manufacturers catch design flaws early, saving time and resources in the long run.
Shortened Lead Times
3D printing significantly shortens lead times for mold production. Traditional methods can take weeks or even months to complete a mold, whereas 3D printing can produce a finished mold in a matter of days. This speed allows manufacturers to respond quickly to market demands and reduces the overall time to market for new products. Faster lead times also enable more agile production processes, allowing companies to quickly adapt to changing consumer preferences or unexpected production challenges.
Cost-Effective
3D printing is a cost-effective alternative to traditional mold-making. The reduction in lead times and the ability to quickly validate designs translate to lower labor and material costs. Additionally, 3D printing eliminates the need for expensive tooling and machining, further reducing production costs. This cost-effectiveness is particularly beneficial for small and medium-sized enterprises (SMEs) that may not have the budget for traditional mold-making processes. By leveraging 3D printing, these companies can compete more effectively in the market.
Customization
Traditional mold-making methods can be limiting when it comes to complex designs. However, 3D printing allows for the creation of intricate and highly detailed molds that would be challenging or impossible to achieve using conventional techniques. This capability is especially valuable in industries where product differentiation and customization are key competitive advantages. Manufacturers can easily create customized molds tailored to specific product requirements, leading to more innovative and unique offerings.
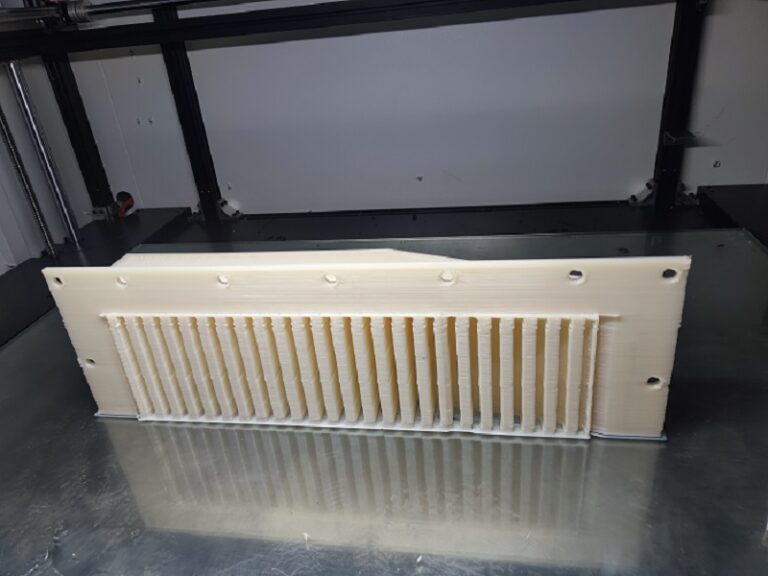
3D Printed Plastic Molds Materials
A broad range of thermoplastics can be injected into 3D printed molds. Here are some of the most commonly used materials:
PP (Polypropylene)
PP is a versatile plastic known for its chemical resistance and low cost. It is widely used in automotive, packaging, and consumer goods industries. PP’s ability to withstand harsh chemical environments makes it suitable for applications where durability and longevity are crucial.
TPE (Thermoplastic Elastomer)
TPE combines the properties of rubber and plastic, making it ideal for applications requiring flexibility and durability. It is commonly used in automotive parts, medical devices, and consumer products. TPE’s elasticity and resilience make it perfect for components that need to endure repetitive stress and strain without losing their shape or functionality.
TPU (Thermoplastic Polyurethane)
TPU is known for its elasticity, transparency, and resistance to oil, grease, and abrasion. It is used in applications such as footwear, automotive parts, and industrial products. TPU’s robustness and flexibility make it an excellent choice for parts that need to perform reliably in challenging environments, such as seals, gaskets, and protective covers.
PA (Polyamide)
PA, also known as nylon, offers high strength and durability. It is used in various applications, including automotive components, textiles, and consumer goods. PA’s excellent mechanical properties, including high tensile strength and resistance to wear and tear, make it suitable for parts that need to maintain structural integrity under heavy loads and friction.
PC-CF (Polycarbonate-Carbon Fiber Composite)
PC-CF is a carbon fiber reinforced polycarbonate composite. It is based on PC raw materials and is mixed with 15%-25% carbon fiber. PC-CF offers high strength, stiffness, and thermal stability, making it ideal for demanding applications. The addition of carbon fiber enhances the material’s rigidity and heat resistance, making it suitable for high-performance parts such as automotive components and industrial machinery parts.
PA-CF (Polyamide-Carbon Fiber Composite)
PA-CF, or PAHT-CF, is easy to print with no warping and high Z-axis strength. It is more chemically resistant than most PA grades and can withstand high temperatures up to 150°C. PA-CF is known for its high tensile strength and resistance to harsh chemicals, making it ideal for parts exposed to aggressive environments. This material is particularly well-suited for applications where parts need to endure extreme conditions, such as chemical processing equipment and aerospace components.
3D Printers for Plastic Molds
Selecting the right 3D printer is crucial for producing high-quality plastic molds. Here are three of the best 3D printers for plastic molds:
G5Ultra Pellet 3D Printer
- Printing Size: 500x500x400mm
- Features:
- Nozzle temperature up to 400℃
- Rapid heating of hot bed up to 120℃
- Screw extruder design
- High-speed printing
The G5Ultra Pellet 3D Printer is a desktop, high-speed industrial production system utilizing low-cost thermoplastic pellet feedstocks. It is ideal for smaller-scale production and rapid prototyping. The printer’s compact size and high-speed capabilities make it an excellent choice for businesses looking to quickly produce detailed molds without investing in large-scale equipment.
G12 Pellet 3D Printer
- Printing Size: 1200x1000x1000mm
- Features:
- Nozzle temperature up to 450℃
- Rapid heating of hot bed up to 120℃
- High Flow Screw Extrusion
- Powerful Servo Motor
The G12 Pellet 3D Printer is a large-format pellet extrusion printer capable of printing medium-to-large format parts. It offers robust performance and precise control, making it suitable for producing larger molds. The printer’s ability to handle larger print sizes allows manufacturers to create molds for substantial components, such as automotive body panels and large industrial parts.
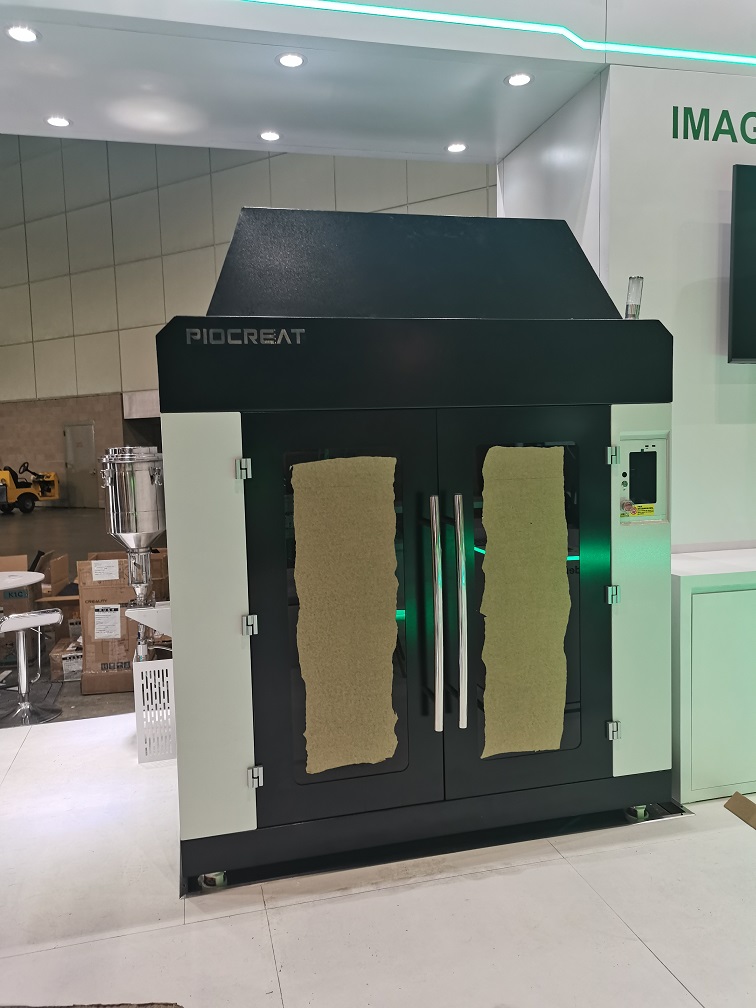
G40 Pellet 3D Printer
- Printing Size: 3725x2500x1330mm
- Features:
- Large working space
- Workbench design
- CNC five-axis head
- High flow screw extrusion design
The G40 Pellet 3D Printer, Piocreat’s largest industrial printer, combines versatility and reliability. It is ideal for industrial-scale projects, offering a large working area and advanced features for complex mold production. The G40’s five-axis head allows for the creation of highly intricate and detailed molds, making it perfect for advanced manufacturing applications where precision is paramount.
Wrapping Up
The integration of 3D printing in the production of large plastic molds is revolutionizing the manufacturing industry. By offering fast validation, shortened lead times, and cost-effective solutions, 3D printing molds enable manufacturers to meet market demands efficiently and economically. With a variety of advanced materials like PP, TPE, TPU, PA, PC-CF, and PA-CF, and cutting-edge 3D printers such as the G5Ultra, G12, and G40 Pellet 3D Printers, the future of mold-making is poised for continued innovation and success.
3D printing molds not only enhances the design and functionality of plastic components but also promotes sustainability by reducing waste and optimizing resource use. As the technology continues to evolve, it will undoubtedly unlock new possibilities for manufacturers, leading to more efficient production processes and higher-quality products.