Table of Contents
3D printing is transforming the aerospace and defense industries by providing innovative solutions for everything from spare parts to complex, customized equipment. With its ability to streamline production, reduce waste, and enable rapid prototyping, additive manufacturing has become a vital tool for enhancing operations. This blog will explore the various applications of 3D printing in aerospace and defense, the advantages it offers, and a case study that highlights its impact.
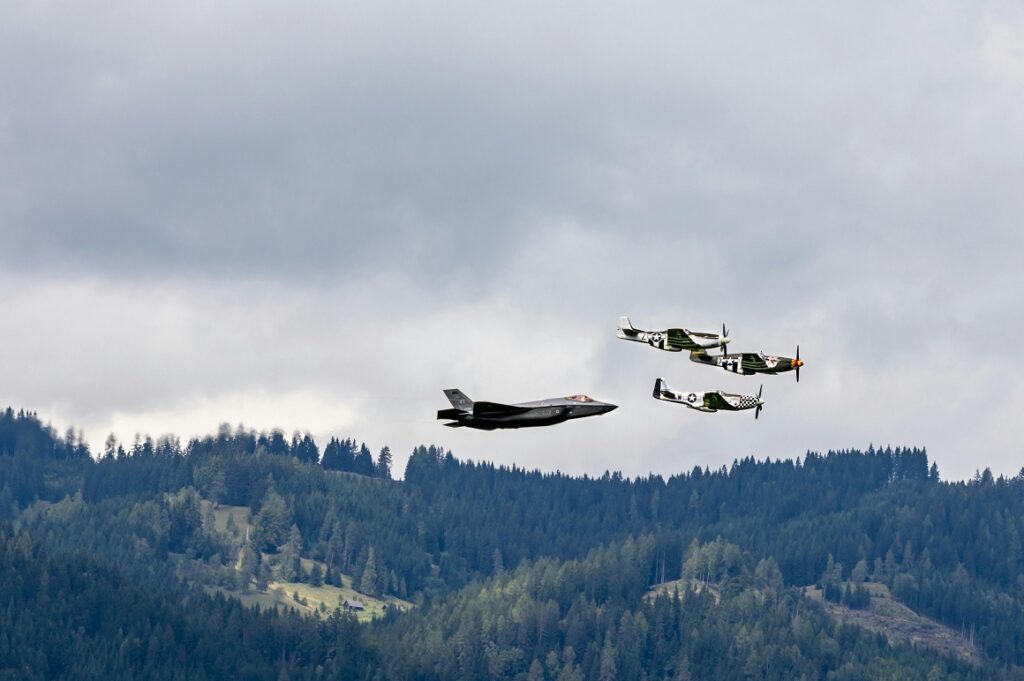
3D Printing Applications in Aerospace and Defense
Spare Parts
One of the most significant applications of 3D printing in the aerospace and defense sectors is the production of spare parts. Aircraft, spacecraft, and defense equipment often require replacement parts, which traditionally would involve lengthy lead times and costly manufacturing processes. With 3D printing, companies can produce spare parts on-demand, reducing both time and cost.
A key benefit of 3D printing spare parts is the ability to create them closer to the point of use. For instance, military units can use 3D printers to manufacture parts in remote locations or during missions, which minimizes downtime and enhances operational readiness. Similarly, aerospace companies can print parts directly at airports or space facilities, ensuring that aircraft and spacecraft remain operational without the need for extended waiting periods for parts to be shipped.
Tools & Equipment Enhancements
In addition to spare parts, 3D printing is widely used to produce specialized tools and equipment for the aerospace and defense industries. Whether it’s custom fixtures, jigs, or tooling for specific manufacturing processes, additive manufacturing allows engineers to design and print tools that are optimized for their tasks.
Custom tooling can be created quickly, often at a lower cost than traditional manufacturing methods. 3D printing also enables the creation of lightweight, durable tools that can withstand the harsh environments typical in aerospace and defense operations. Furthermore, the design freedom offered by 3D printing means that engineers can develop more complex geometries that would be impossible or too expensive to achieve with traditional manufacturing methods.
Advantages of 3D Printing in Aerospace and Defense
The adoption of 3D printing in the aerospace and defense sectors provides a number of distinct advantages:
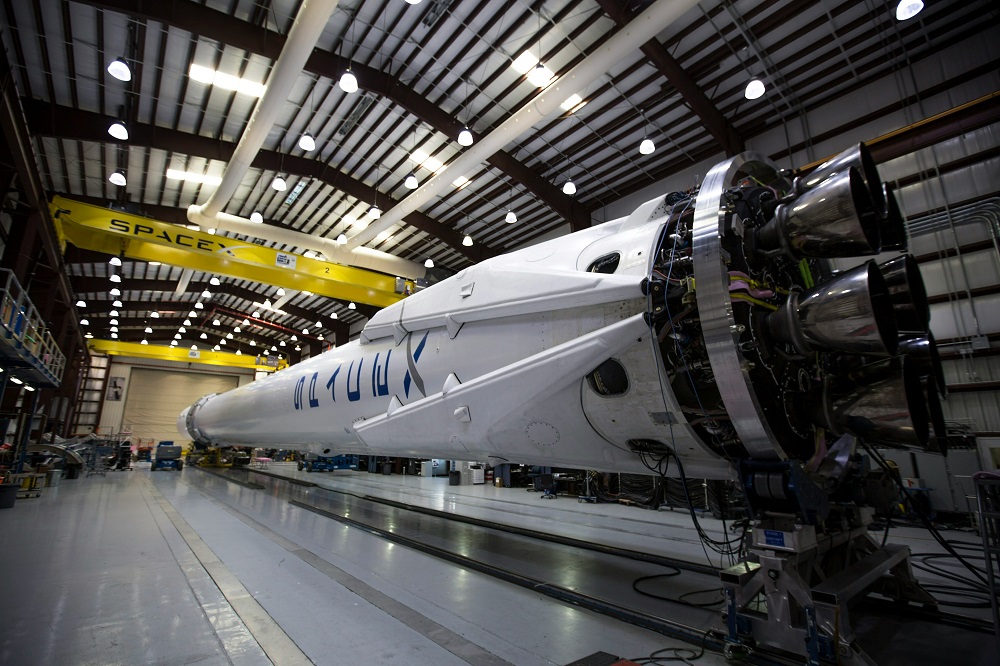
Rapid Prototyping
One of the most significant benefits of 3D printing is rapid prototyping. In industries where time-to-market is critical, the ability to quickly develop and test prototypes is a game-changer. Engineers can design a part, print it, and test its functionality within hours or days, as opposed to the weeks or months that traditional manufacturing processes would take.
This shortened development cycle allows aerospace and defense companies to experiment with new designs more efficiently. Rapid prototyping not only speeds up product development but also reduces the costs associated with creating multiple iterations of a part before finalizing a design.
Waste Reduction
3D printing is an additive manufacturing process, meaning that materials are added layer by layer to create a part. This contrasts with traditional subtractive manufacturing, where materials are removed from a solid block, often resulting in significant waste.
In the aerospace and defense industries, materials such as titanium and other high-performance metals are expensive. 3D printing drastically reduces waste by using only the material needed for the part, making it a more cost-effective and environmentally friendly option.
Customized Equipment
The ability to create customized equipment is a major advantage of 3D printing. In defense applications, where every mission and environment is unique, the need for specialized gear and tools is paramount. 3D printing allows manufacturers to produce equipment tailored to specific requirements, from customized drone parts to advanced military-grade tools.
In aerospace, where precision and optimization are critical, customization helps improve performance. Engineers can tweak designs to enhance aerodynamics or reduce weight, which leads to better fuel efficiency and overall performance in aircraft and spacecraft.
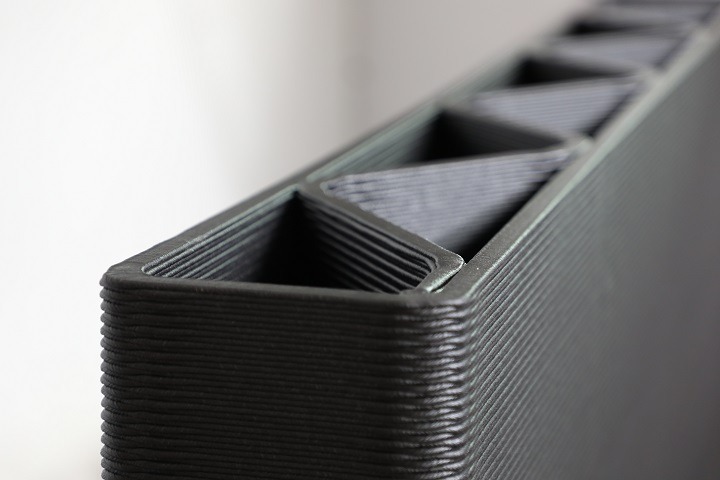
Rapid Product Development
In addition to rapid prototyping, 3D printing facilitates rapid product development by allowing companies to create functional parts faster. Once a design is finalized, it can be quickly printed and integrated into the final product. This capability is especially useful in defense, where new technologies need to be deployed quickly to meet evolving threats or operational needs.
The ability to manufacture parts and products at a faster pace provides a competitive advantage for aerospace and defense companies, allowing them to stay ahead in innovation.
Freedom of Design
Traditional manufacturing methods often impose limitations on design due to the constraints of tooling, molds, and machining. 3D printing eliminates many of these limitations, offering freedom of design. Engineers can create complex geometries, internal structures, and lightweight designs that were previously impossible or too costly to manufacture.
This freedom of design is particularly advantageous in aerospace, where reducing weight without compromising strength is critical for fuel efficiency and performance. 3D printing allows engineers to optimize parts for both strength and weight, leading to more efficient aircraft and spacecraft.
Case Study: Aerospace Company Adopts Pellet Extrusion 3D Printing for Large Thermoforming Molds
An aerospace company recently adopted pellet extrusion 3D printing to produce large-scale thermoforming molds, significantly reducing both costs and lead times. The company used the PioCreat G40 Pellet 3D Printer, a large-scale industrial printer designed for complex, high-volume projects.
Key Features of the PioCreat G40 Pellet 3D Printer:
- Large Build Volume: With a build size of 3725×2500×1330mm, the G40 can handle large-format printing tasks with ease, making it ideal for the aerospace industry.
- High Flow Screw Extrusion: The printer boasts a material flow rate of 25kg per hour, allowing for rapid production of large parts.
- Nozzle Temperature Up to 450°C: This high-temperature capability enables the use of advanced thermoplastics and composites, which are critical for aerospace applications.
- CNC Five-Axis Manufacturing Integration: The G40 combines 3D printing with CNC technology, allowing for the production of highly detailed and precise molds.
By using large-format pellet extrusion 3D printing, the aerospace company was able to produce molds for thermoforming at a fraction of the time and cost required by traditional methods. The molds, which would have taken weeks to manufacture using conventional processes, were produced in days, allowing the company to accelerate its production schedule.
Additionally, the cost savings were significant, as the use of pellet-fed extrusion technology reduced material costs by up to 60% compared to filament-based 3D printing. This case study illustrates the potential for 3D printing to revolutionize manufacturing processes in the aerospace industry, offering both economic and operational benefits.
Looking Forward
3D printing is playing a transformative role in the aerospace and defense industries by enabling rapid prototyping, reducing waste, and allowing for customized equipment and rapid product development. With its ability to create complex designs that were previously impossible with traditional manufacturing methods, 3D printing offers a range of advantages that improve efficiency, cost-effectiveness, and overall performance.
The PioCreat G40 Pellet 3D Printer is an example of how large-scale 3D printing technology is being utilized to meet the demands of the aerospace sector. By adopting innovative additive manufacturing technologies, aerospace and defense companies can continue to push the boundaries of innovation and maintain their competitive edge in the global market.