Table of Contents
Thermoplastic Polyurethane (TPU) is gaining popularity in 3D printing due to its excellent mechanical properties and versatility. Whether you’re a beginner exploring materials for your first print or an expert looking for high-performance solutions, TPU offers a wide range of applications in fields like automotive, aerospace, and medical devices. In this blog, we’ll delve into the properties of TPU, how it works with Fused Granulate Fabrication (FGF) 3D printing technology, and its applications across industries.
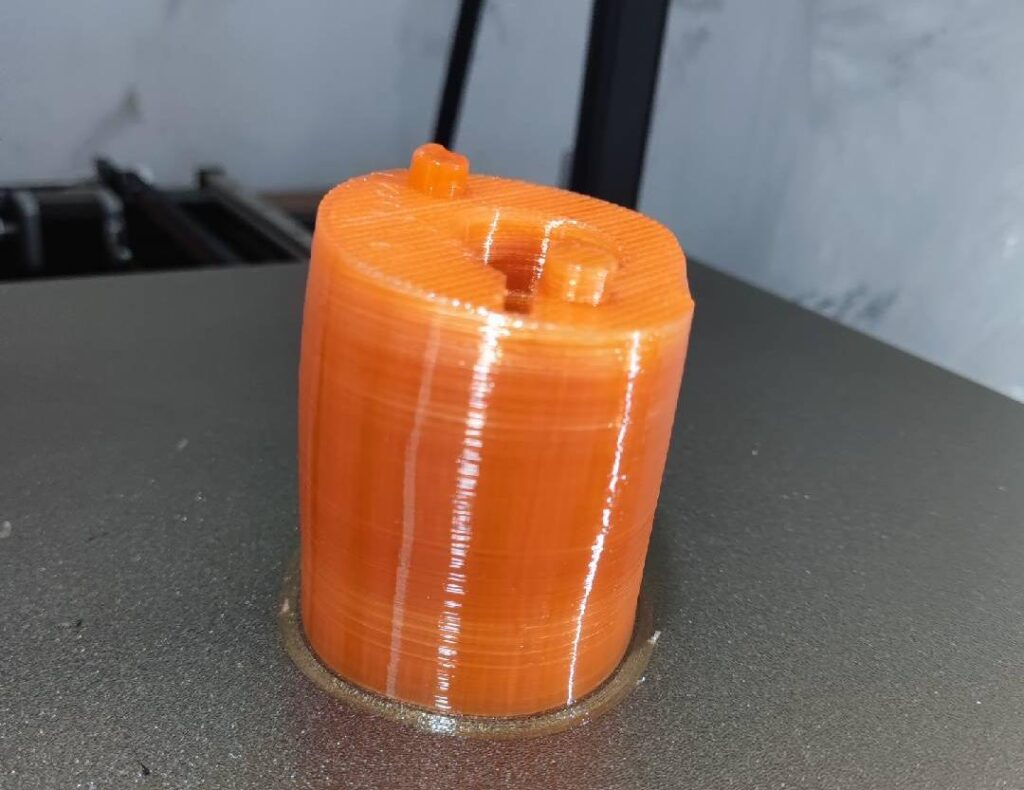
What is TPU?
Thermoplastic Polyurethane (TPU) is a flexible, durable, and elastic material commonly used in 3D printing for parts that require strength, flexibility, and resistance to wear. Unlike rigid plastics such as PLA or ABS, TPU provides a rubber-like texture, making it an ideal choice for printing parts that require both softness and durability. TPU is a member of the thermoplastic elastomer (TPE) family, and it combines the elasticity of rubber with the processing advantages of thermoplastics.
TPU can be used in 3D printing through a variety of technologies, but its compatibility with FGF 3D printing allows for the production of large-scale, industrial-grade parts with high precision.
TPU Properties
Chemical Composition of TPU
TPU is composed of alternating soft and hard segments that give it both elasticity and toughness. The material is typically based on either polyester or polyether chemistry. Polyester-based TPU is known for its excellent mechanical properties, chemical resistance, and durability, while polyether-based TPU offers superior hydrolysis resistance.
TPU’s unique molecular structure results in its flexibility, impact resistance, and high elongation at break, making it suitable for products that need to endure continuous stress or exposure to harsh environments.
Physical Properties of TPU
TPU offers a range of properties that make it stand out in 3D printing applications:
- High mechanical strength: TPU can withstand significant stress and strain without deforming, making it ideal for applications where strength and flexibility are essential.
- Elasticity: TPU has a high degree of flexibility, enabling it to return to its original shape after stretching or compressing.
- Wear resistance: The material has excellent resistance to wear and tear, making it suitable for parts that need to endure repeated use.
- Oil resistance: TPU exhibits good resistance to oils and greases, which is valuable in industrial environments where exposure to such substances is common.
- Abrasion resistance: TPU can endure rough handling, making it perfect for parts subjected to friction or constant movement.
These properties make TPU a versatile material for both functional and aesthetic applications in industries requiring durable and resilient components.
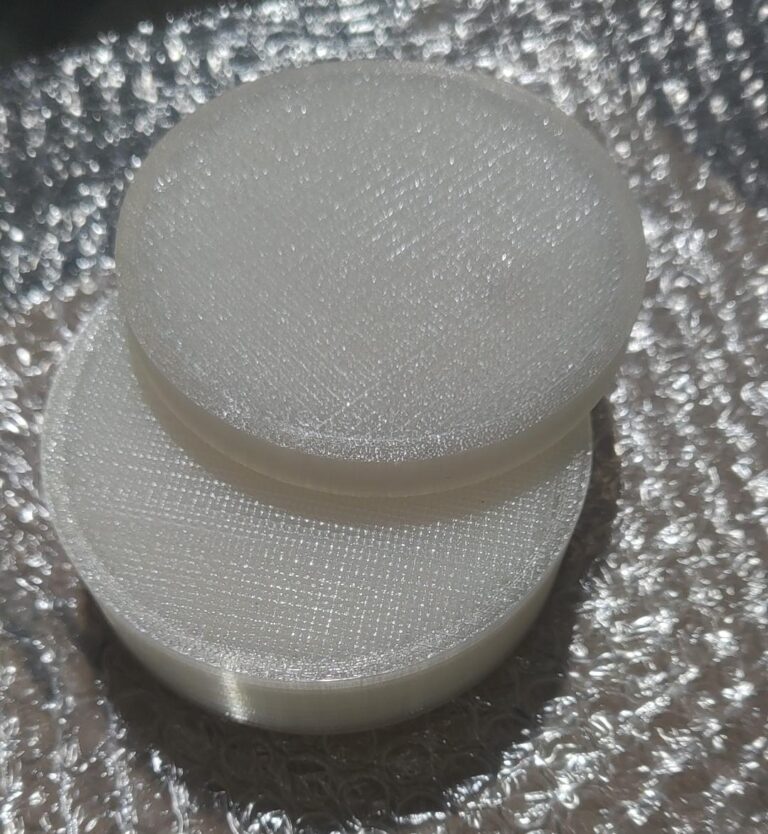
3D Printing TPU with FGF 3D Printing
What is Fused Granulate Fabrication (FGF)?
Fused Granulate Fabrication (FGF) is an industrial-grade 3D printing process that uses plastic pellets as feedstock, rather than traditional filament. The pellets are fed into an extruder, melted, and deposited layer by layer to create the final object. This method is particularly useful for large-scale printing projects, as it allows for faster production and lower material costs compared to filament-based printing.
FGF printing is ideal for TPU because it enables the use of original thermoplastic pellets, ensuring that the material retains its superior mechanical properties and performance. The high-speed extrusion process can maintain TPU’s unique attributes, such as elasticity, flexibility, and toughness, during the 3D printing process.
Advantages of FGF Printing with TPU
- Cost-effective: FGF printing uses pellets, which are generally more affordable than filament. This makes it a cost-efficient option for large-scale production or industrial applications.
- Enhanced material properties: FGF allows for precise control over the extrusion and cooling process, ensuring the printed TPU components maintain their elasticity, toughness, and strength.
- Versatility in material usage: With FGF printers, users can switch between various materials, including TPU, which makes the process highly adaptable for different applications.
- Speed and scale: FGF technology is capable of producing large-scale parts more quickly than traditional 3D printing methods, making it ideal for industries like automotive and aerospace.
TPU Pellets for FGF Printers
Piocreat’s TPU pellets are specifically designed for FGF 3D printing. These pellets are available in transparent, translucent, or colored forms and are free of plasticizers, ensuring that the material offers optimal performance for demanding applications.
Key Characteristics of Piocreat TPU Pellets:
- High mechanical strength: Ensures durability in applications requiring long-term use and stress resistance.
- High toughness: Provides the necessary elasticity for flexible applications while maintaining structural integrity.
- Wear resistance: Makes TPU ideal for parts that are subject to constant movement or friction, such as gears or protective cases.
- Oil resistance: Ensures that printed parts can withstand exposure to oils, greases, and other industrial chemicals.
These features make Piocreat’s TPU pellets an excellent choice for industries looking to 3D print components that combine flexibility and strength.
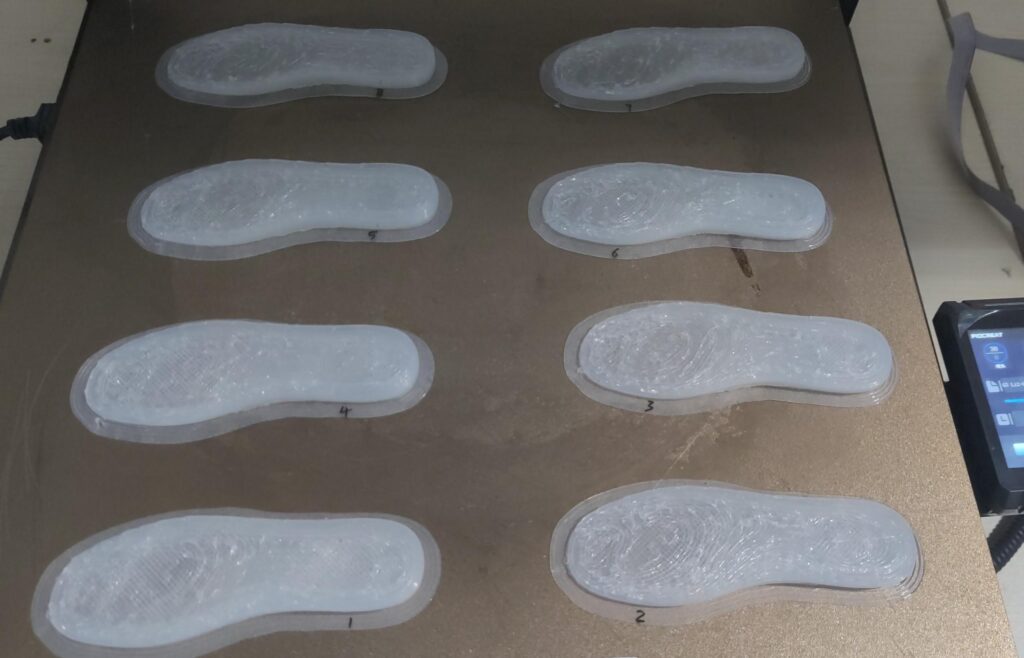
Applications of TPU 3D Printing
Thanks to its unique properties, TPU is widely used across several industries, each benefiting from the material’s versatility, durability, and elasticity.
1. Rapid Prototyping
TPU is an excellent material for rapid prototyping due to its flexibility and strength. Engineers and designers can create functional prototypes that accurately mimic the final product’s mechanical properties, enabling thorough testing and design refinement. This is particularly valuable in industries such as automotive and aerospace, where parts often need to withstand high stress and impact during real-world use.
2. Automotive
In the automotive sector, TPU is used to print parts like gaskets, seals, and shock absorbers. The material’s flexibility and oil resistance make it ideal for parts exposed to constant motion and harsh environments. 3D printing with TPU also allows for the customization of components, such as dashboard elements or protective covers, enhancing both functionality and aesthetics.
3. Aerospace
The aerospace industry demands lightweight yet strong materials, and TPU fits the bill. Components such as protective covers, insulation parts, and shock-absorbing elements can be produced using 3D printing. TPU’s durability and wear resistance ensure that parts meet the high-performance standards required in aerospace applications.
4. Medical Devices
In the medical field, TPU is used to print prosthetics, orthotics, and medical models. The material’s elasticity allows for the creation of comfortable, flexible prosthetic limbs and custom-fit orthotic devices. Moreover, TPU’s biocompatibility ensures that it can be safely used for medical applications.
5. Manufacturing Aids
In industrial settings, TPU is often used to create custom tooling, jigs, and fixtures. These manufacturing aids need to be both tough and flexible to accommodate various production needs. TPU’s wear resistance and flexibility make it ideal for creating tools that can withstand continuous use in an industrial environment.
Conclusion
TPU is a versatile material that offers a range of benefits in 3D printing, from flexibility and toughness to wear resistance and oil resistance. When paired with Fused Granulate Fabrication (FGF) 3D printing, TPU pellets like those offered by Piocreat enable the creation of high-performance parts for industries such as automotive, aerospace, and healthcare. Whether you’re engaged in rapid prototyping, producing functional parts, or exploring creative design possibilities, TPU in 3D printing provides the performance and reliability required for diverse applications.
For beginners, TPU offers a flexible and forgiving material to work with, while experts can exploit its advanced mechanical properties to push the boundaries of 3D printing technology.