Table of Contents
Additive Manufacturing (AM) is revolutionizing furniture production by enabling unparalleled customization, design flexibility, and sustainability. Among the various 3D printing technologies, pellet extrusion has emerged as the method of choice. This technique utilizes pellets and shredded recycled plastic, offering both financial and environmental advantages for a wide range of applications. You can reduce material costs by over 60%, and it facilitates the production of large-scale pieces quickly and affordably, making end-use furniture production feasible.
Can a 3D Printer Make Furniture?
Absolutely! With advancements in large-scale 3D printing, creating functional and stylish furniture with a 3D printer is not only possible but also increasingly common. By using a pellet 3D printer, manufacturers can produce everything from chairs and tables to intricate home decor. These printers can handle large-scale designs, ensuring that even substantial pieces are printed efficiently.
Large-scale 3D printing has evolved to the point where it can compete with traditional manufacturing methods. The primary advantage is its ability to produce complex geometries that are difficult or impossible to achieve with conventional techniques. For instance, intricate lattice structures that offer both strength and aesthetic appeal can be created with ease using a 3D printer.
Another significant advantage is the reduction in assembly requirements. Traditional furniture often comprises numerous parts that need to be assembled, which adds to labor costs and production time. In contrast, 3D printed furniture can be produced as a single piece or with minimal assembly, streamlining the manufacturing process.
What Material is Used for Pellet 3D Printing Furniture?
When it comes to materials for 3D printed furniture, two popular choices are PETG and ABS pellets.
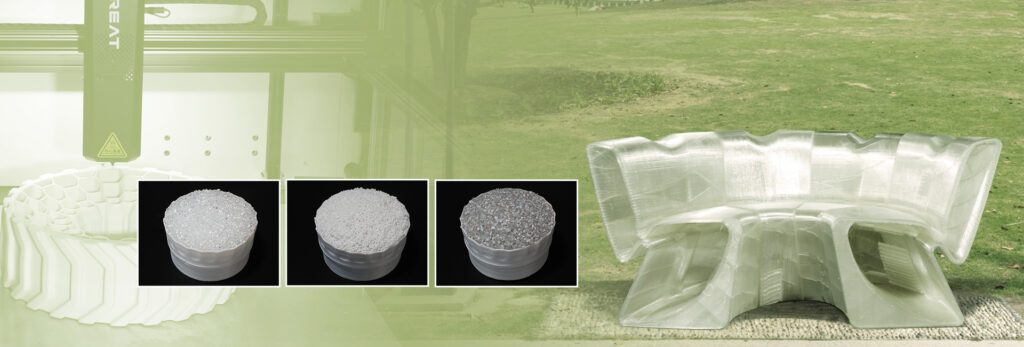
PETG Pellets
PETG (Polyethylene Terephthalate Glycol) pellets are known for their strength, durability, and ease of printing. They are ideal for producing robust furniture pieces that can withstand everyday use. PETG is also recyclable, aligning with sustainable production goals.
PETG’s properties make it an excellent choice for furniture that needs to endure everyday wear and tear. It has high impact resistance, ensuring longevity even in high-traffic environments. Moreover, PETG is hygroscopic, meaning it resists moisture absorption, making it suitable for outdoor furniture as well.
ABS Pellets
ABS (Acrylonitrile Butadiene Styrene) pellets offer excellent mechanical properties and high impact resistance. This material is perfect for furniture that needs to endure significant wear and tear. ABS is also relatively easy to work with, providing a smooth finish for printed items.
ABS is renowned for its toughness and ability to withstand various environmental conditions. It’s commonly used in the automotive industry for similar reasons, which makes it an excellent material for furniture that requires durability. Additionally, ABS can be post-processed easily to achieve a high-gloss finish, adding to the aesthetic appeal of the furniture.
Benefits of 3D Printed Furniture with Pellet Extrusion
Higher Customization Flexibility
One of the standout benefits of 3D printed furniture is the ability to customize designs with ease. Manufacturers can tailor each piece to specific customer preferences, resulting in unique, bespoke items that cater to individual tastes.
Customization goes beyond aesthetics; it includes functionality as well. For example, ergonomic chairs can be designed to fit the exact body dimensions of an individual, providing personalized comfort. This level of customization is challenging to achieve with traditional manufacturing methods without incurring significant costs.
Faster Turnaround Time
Traditional furniture manufacturing can be time-consuming, but pellet 3D printers significantly speed up the process. The ability to produce large-scale pieces quickly means reduced lead times and faster delivery to customers.
Speed is a crucial factor in the modern market, where consumers expect quick turnaround times. 3D printing can reduce the production time from weeks or months to just days, depending on the complexity of the design. This rapid production capability allows businesses to respond swiftly to market demands and trends, maintaining a competitive edge.
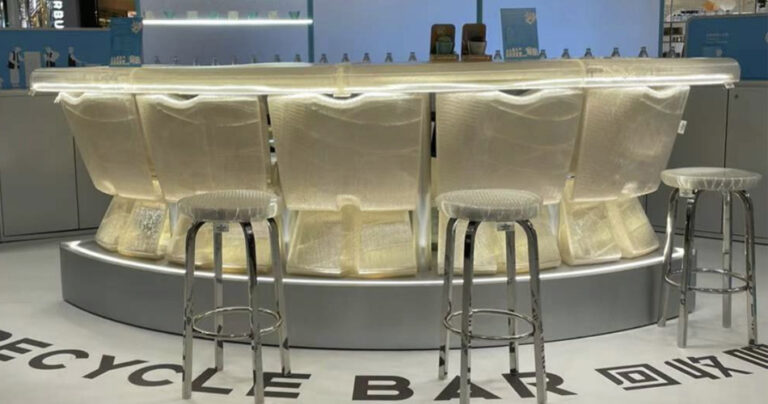
Design Freedom - Thinking Outside the Box
3D printing allows designers to experiment with innovative shapes and structures that would be impossible or too costly to achieve with traditional methods. This freedom leads to more creative and functional furniture designs.
For instance, organic shapes that mimic natural forms can be easily produced using 3D printing. These designs not only enhance the aesthetic appeal but also offer functional benefits such as improved structural integrity and material efficiency. The ability to create such unique designs sets 3D printed furniture apart from mass-produced items.
Less Production Wastage
Pellet extrusion is an efficient process with minimal waste. Unlike subtractive manufacturing, which cuts away material, additive manufacturing builds furniture layer by layer, using only the necessary amount of material. This efficiency reduces costs and environmental impact.
Waste reduction is a significant advantage in today’s environmentally conscious world. Traditional manufacturing processes often result in a considerable amount of scrap material, which adds to both cost and environmental burden. 3D printing’s additive nature ensures that almost all the material used goes into the final product, minimizing waste.
Detect Potential Design Flaws
The digital nature of 3D printing enables designers to prototype and test furniture before committing to full-scale production. This capability helps identify and rectify design flaws early, ensuring higher quality final products.
Prototyping is an integral part of the design process, allowing for the testing of various iterations and modifications without the need for expensive tooling changes. By identifying potential issues early in the development process, companies can save time and resources while ensuring that the final product meets the desired specifications and quality standards.
Higher ROI and Lower Production Cost
The cost savings from reduced material waste and faster production times translate into a higher return on investment for manufacturers. Pellet 3D printing is a cost-effective method that lowers overall production costs while maintaining high quality.
In addition to direct cost savings, the flexibility and efficiency of 3D printing enable manufacturers to bring products to market more quickly, capitalize on trends, and meet customer demands with less financial risk. This agility can lead to increased sales and profitability.
More Sustainable
Using recycled plastic pellets in 3D printing aligns with sustainable manufacturing practices. This approach not only reduces reliance on virgin materials but also contributes to waste reduction by repurposing plastic that would otherwise end up in landfills.
Sustainability is becoming increasingly important to consumers, and businesses that prioritize eco-friendly practices can enhance their brand reputation and appeal to a broader audience. 3D printing with recycled materials supports a circular economy, where products are designed with their end-of-life in mind, promoting recycling and reuse.
Best 3D Furniture Printers
G12 Pellet 3D Printer
- Printing Size: 1200*1000*1000mm
- Features:
- Nozzle temperature up to 450℃
- Rapid heating of hot bed up to 120℃
- High Flow Screw Extrusion
- Powerful Servo Motor
The G12 Pellet 3D Printer is a large-format printer ideal for creating medium-to-large furniture pieces efficiently. Its high-temperature capabilities and rapid heating ensure that a wide range of materials can be used, making it versatile for different design requirements.
G40 Pellet 3D Printer
- Printing Size: 3725*2500*1330mm
- Features:
- Large working space
- Workbench design
- CNC five-axis head
- High flow screw extrusion design
The G40 Pellet 3D Printer, PioCreat’s largest industrial printer, combines additive and CNC five-axis manufacturing, making it a versatile and reliable option for industrial-scale furniture production. The CNC capabilities allow for precise machining, enhancing the functionality and finish of the printed pieces.
Wrapping Up
3D printed furniture with pellet extrusion is transforming the furniture industry, offering unmatched customization, faster production times, and significant cost savings. By utilizing PETG and ABS pellets, manufacturers can produce durable, sustainable, and innovative furniture designs. The G12 and G40 Pellet 3D Printers exemplify the best in large-scale 3D printing technology, pushing the boundaries of what’s possible in furniture manufacturing.
The future of furniture manufacturing is here, and it’s additive. Embracing 3D printing technology not only enhances production capabilities but also aligns with the growing demand for sustainable and customized products. Whether you’re a manufacturer looking to innovate or a consumer seeking unique and eco-friendly furniture, 3D printed furniture with pellet extrusion offers exciting possibilities.